Induction motors at the starting draw higher current than normal operating current. This starting current is represented as kilo volt ampere power.
Each motor has its starting power and is set on the motor nameplate as KVA code.
Table of Contents
KVA code of electric motors meaning
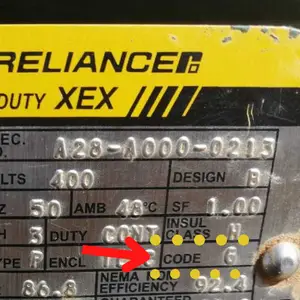
The Motors KVA code is represented on the nameplate as a letter referring to the motor starting kVA.
Depending on the horsepower (H.P.) of the motor, the KVA code is used to describe the (locked rotor ampere) LRA in KVA.
There are several code letters for motors with locked rotor KVA per horsepower that range from lower than 3.14 to higher than 22.4 KVA per horsepower.
The letters indicate the Kilo Volt Ampere that is drawn by the motor when its rotor is locked reported in kVA / HP.
Code letters are ranged from A to V, Code V motors have the highest starting kVA value while Code A motors have the lowest. The higher the KVA code the higher the motor starting current.
Why Do We Use KVA Code?
By using the KVA code, we can easily calculate the starting current of a motor based on its letter code.
Knowing the starting current of the motor, which is represented as KVA, is important to ensure that the network is capable of starting the motor with an acceptable voltage drop, and to ensure the overcurrent protection won’t trip during the starting.
When replacing a motor, the KVA code should be noted. It’s important to note that if you replace a lower code letter with a higher code letter, other electrical equipment upstream, such as the motor starter, may require a change.
Motors with higher KVA codes may require a starting method, like a soft starter, to decrease the starting current. A higher starting current causes a higher voltage drop affects other loads and can cause them to stop.
Once we had a large induction motor with a high starting current installed in a water plant at my work, the starting of the motor caused the other motor to stop due to an under-voltage fault, however, the motor has a soft starter. To overcome this issue we replaced the transformer with a larger one.
I’ve written a detailed article about, What are different types of motor starting methods. you can read it for more information.
Motor KVA Code Calculation With Example
Using the KVA code table below, the KVA drawn by a motor is given by the formula:
Motor KVA = Motor power (HP) * KVA value (from the table)
From the below table, a 10-hp induction motor would draw:
- 10 (hp) * 3.14 (for A KVA code) = 31.4 kVA, if its code letter is A.
- If the same motor KVA code letter is D it would draw 10 * 4.3 = 43 kVA
The below table gives the code letters and the values of KVA drawn in starting.
Motor KVA Code Table
In order to classify motors based on the ratio of the locked rotor kVA to the horsepower, the National Electrical Manufacturer’s Association (NEMA), which lays out the design standards for motors, has established the NEMA Code letters.
It is possible to determine the starting kVA needed to start a motor at full voltage either from the motor nameplate or by finding out from the manual provided by the manufacturer.
CODE LETTER’S | KVA/HP WITH LOCKED ROTOR | APPROXIMATE MID-RANGE VALUE |
A | 0 – 3.14 | 1.6 |
B | 3.15 – 3.55 | 3.3 |
C | 3.55 – 3.99 | 3.8 |
D | 4.0 – 4.49 | 4.3 |
E | 4.5 – 4.99 | 4.7 |
F | 5.0 – 5.59 | 5.3 |
G | 5.6 – 6.29 | 5.9 |
H | 6.3 – 7.09 | 6.7 |
J | 7.1 – 7.99 | 7.5 |
K | 8.0 – 8.99 | 8.5 |
L | 9.0 – 9.99 | 9.5 |
M | 10.0 – 11.19 | 10.6 |
N | 11.2 – 12.49 | 11.8 |
P | 12.5 – 13.99 | 13.2 |
R | 14.0 – 15.99 | 15.0 |
S | 16.0 – 17.99 | |
T | 18.0 – 19.99 | |
U | 20.0 – 22.39 | |
V | 22.4 – and up |
What Does KVA Code G Means?
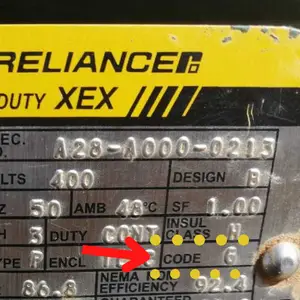
The kVA code letters in the National Electrical Code (NEC) represent a range of kilovolt-amps per horsepower during the locked rotor (starting) of induction motors.
KVA code G means this motor can consume KVA power ranging between 5.6 to 6.29 kVA/hp at its starting.
This value is used to calculate the motor’s kVA at startup as follows:
For a motor with a nameplate rating of 300 HP and a KVA code of G, the apparent power at startup (when the rotor speed is zero) will range from:
5.6×300=1680 kVA
to
6.29×300=1887 kVA
Does Motor KVA Code Affect the Performance Of Motor?
KVA Code didn’t affect the performance of motors, it’s just an indicator of how much current the motor draw at starting. Using the KVA code enables you to determine what type of reduced voltage starter is required for the motors.
It’s more crucial and common to use a motor starting method for higher horsepower three-phase motors, mostly because three-phase motors have higher KVA.
No matter what the KVA code of a motor is, the performance of the motor remains the same.
For more details about motor starting methods read my articles:
What Is The Motor LRA(Locked Rotor Ampere)?
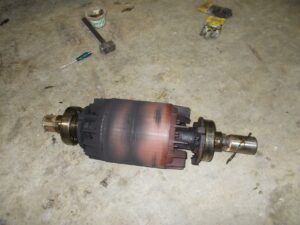
Locked Rotor Amps (LRA) is the maximum current a motor draws when starting from a standstill with full voltage applied to the stator. This surge occurs because the rotor is not yet moving, so no back electromotive force (EMF) is generated to oppose the incoming current.
Importance of LRA
LRA plays a key role in motor circuit design. It helps in selecting:
- Circuit breakers
- Starters
- Over-current protection devices
These components must handle the high initial current without tripping or damage.
Induction Motor Behavior at Startup
At startup, the slip of an induction motor is at its maximum value (s = 1), meaning the rotor is stationary while the stator creates a rotating magnetic field.
- Maximum Slip (s = 1): The magnetic field induces the highest possible voltage in the rotor coils or bars.
- High Rotor Current: This results in significantly higher currents in the rotor, generating heat since no mechanical power is produced (the shaft is locked).
In this state, the motor behaves similarly to a transformer, with energy transferred across the air gap entirely dissipated as heat.
Measuring LRA
By measuring the locked rotor current, engineers can determine the equivalent circuit components of an induction motor. This helps in understanding the motor’s behavior and optimizing its performance.
Stress on Rotor Components
The high current during startup places stress on the rotor coils or bars, which must withstand this load without failure. As the motor starts, slip decreases, and the rotor currents reduce, transitioning the motor to normal operation.
How to convert LRA to hP?
Yes, is it possible to convert locked rotor amper (LRA) to HP using the given formula: HP=LRA (Locked Rotor Ampere’s) x Volts / 746Watts
Let’s Calculate the HP for Three Phase Motor when LRA is Known:
LRA = 22.5
Voltage (Three Phase) = 440V
Put the given values in the formula:
HP=22.5 x 440 / 746Watts
HP=9900 / 746 Watts
Answer =13HP
What Is the Difference Between FLA and LRA?
Locked Rotor Amps (LRA): This is the maximum current a motor will draw when full voltage is applied during startup.
Full Load Amps (FLA): This is the maximum current a motor will draw under full load and normal operating conditions.
Key Differences and Uses:
- FLA is used to select motor starters, protection devices, and cables for safe operation and control.
- LRA helps in choosing overcurrent protection to prevent tripping during startup.
While FLA is based on the motor’s power rating and actual load, LRA reflects the initial surge of current during startup. FLA is typically listed on the nameplate as a current value, while LRA is represented as a letter code.
Do LRA Of Motor Matter?
The LRA of a motor is important because it helps in selecting the right upstream breakers, starting method, and overcurrent protection devices. By knowing the LRA and the motor’s acceleration time, you can ensure that the system can handle the high inrush current during startup without unnecessary tripping or damage.
We ensure that the circuit breaker, fuse, or overcurrent protection device can supply the locked rotor amps for the duration required to bring the motor load up to speed and that it will trip if the locked rotor amps exceed the permissible stall period.
LRA should never be compared to an overcurrent device’s continuous current rating. Locked Rotor Current is a decent estimate of the short circuit current added by a motor to a power system short circuit.
Don’t Leave Empty-Handed!
Install my Free Android App on Google Play:
Electrical Cables Most Common Tables “Cables Tables”
And, my Electrical Calculations App “Fast Electrical Calculator”
Discover more great content by subscribing to My channel
Looking to stay ahead of the game in the world of electrical engineering? Subscribe to my YouTube channel and gain access to exclusive content you won’t find anywhere else!
The staff I recommend
(Amazon Affiliate Links to products I believe are high quality):
- Economy 120 Volt/60Hz AC Power Source – Step-Down Voltage & Frequency Converters 1800W
- UNI-T Digital Multimeter Tester UT139C
- 50-Amp Extension Cord for RV “100ft”
- Voltage Stabilizer 110/220v
- Hair Dryer “best selling“
- TOSHIBA EM131A5C-BS Countertop Microwave Ovens
Disclaimer: This contains affiliate links to Amazon products. I may earn a commission for purchases made through these links.