Motors are electric equipment that draw current to run, each motor has a designed value of rated current to draw in normal operation.
If the motor, for any reason, draws current greater than the rated current value, we call this excess current motor overcurrent.
Table of Contents
Motor overcurrent effect
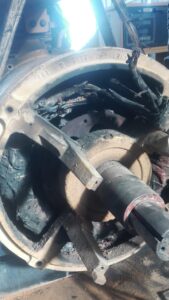
Overcurrent in motors, cables, transformers, or any electrical equipment, is an unusual condition and can be a destructive fault.
Overcurrent, if the motor is not protected against, increases the motor winding temperature and burns out the motor (or any other electrical equipment).
If the overcurrent value is not very large, it can cause the motor to overheat. If the situation still for a longer time the motor will burn out.
The point is, that the effect of the overcurrent depends on its value and duration.
A large overcurrent value for a very short period, i.e. the protection device activated at the right timing, will cause no harm to the motor.
A smaller value for a long time will increase the motor temperature, overheat it, and burn it out.
I have written an article about Motor Temperature Rise, read it for more information.
What causes Motor overcurrent?
To maintain its torque, a motor draws more current for many reasons,
- Low supply voltage (voltage drop)
- Low Resistance
- Mechanical Overload
- Over-Heating
- Contamination
- Bad bearings
- Phase loss
I have written a detailed article about Overcurrent, Check It Out for more information.
Let’s discuss motor overcurrent causes one by one,
Under voltage (voltage drop)
Electric motors are fixed power equipment, when the voltage drops, the motor draws more current to produce its torque.
A motor draws a specific quantity of electricity from the line to drive its mechanical load attached to the shaft. The motor’s power consumption is roughly correlated to the voltage-current (amps).
Only when an increase in current surpasses the nameplate current rating of the motor does it pose a threat to the motor?
Motor voltage drop causes the motor temperature to increase due to the higher current value, if the motor protection device fails to trip the motor will burn out.
low insulation resistance
Low insulation resistance is likely the most frequent and challenging factor in motor failure. Low resistance is brought on by the windings’ insulation deteriorating from issues like overheating, corrosion, or physical harm due to overcurrent.
This results in inadequate insulation between the conductors or motor windings, which can eventually lead to leaks short circuits, and motor failure.
Motors in wet locations face the issue of insulation resistance decrease. Moisture affects the insulation and can cause a short circuit. This is not the case for motors only, moisture can damage motors as well as generators and transformers.
I have written a detailed article about Motors in Wet Locations, Read It For More Information.
Motor overload
Overload is one of the main reasons electric motors fail. Mechanical loads as well as damaged bearings are the main sources of motor overloading.
It occurs when the motor’s output torque is insufficient to move the load. The motor draws overcurrent to produce its rated torque.
The mechanical overload of a motor refers to, the non-electrical problems, usually related to loads, that cause the motor to draw overcurrent.
This excess current will damage the motor’s windings and ultimately cause the motor to fail.
The service factor rating on the motor’s nameplate will indicate how much overload your motor can handle for a brief duration.
NEMA advises operating the motor at no less than 90 percent of nameplate-rated voltage in under-voltage conditions and 110 percent in over-voltage conditions.
Over-Heating
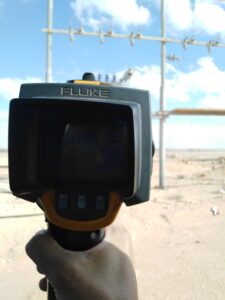
Thermal imaging is a good way to check motor temperature. We use it in my work, it’s perfect.
Approximately 55% of all failures in insulating parts of motors are caused by overheating.
The cause of excessive heating can be working on continuously overcurrent conditions, either poor power quality or a high degree of operating temperature.
There is a 50% reduction in the insulation life of a motor for every 10 degrees Celsius that the temperature rises over the motor. For more information about motor insulation, read my article here.
For more details about motor temperature rise, read my other article here.
Contamination
One of the reasons why motors draw overcurrent is contamination by dust, grime, and chemicals.
High levels of vibration and wear are caused by objects that become stuck within the motor and damage the bearing raceways and balls It can be caused by a drawn overcurrent within the motor.
This issue is a common one in case of a motor not working for a long time, and not well stored.
It can also prevent the cooling fan from operating, restricting the motor’s capacity to control its temperature and increasing the risk of overheating.
I have seen many cases where motor temperature increases due to plastic bags on the cooling fan cover. We use thermal imaging to detect such issues.
I have written a detailed article about how temperature affects electric equipment. You can find it here.
Bad Bearings
Motor bearing damage is one of the most common motor overcurrent causes I have ever seen in my work as an electrical engineer.
Motor bearings unquestionably have a significant impact on how well your electric motor works. Bearing is used to make the rotation of the rotor smooth by reducing friction.
There is a strong likelihood that a failed bearing may be the cause of a sudden motor failure due to the higher friction as well as the higher current.
When a bearing fails, the motor becomes jammed and draws excessive current, which leads to burned motor windings and motor failure.
Read also my article about Overcurrent here.
How to tell if a motor is drawing an overcurrent?
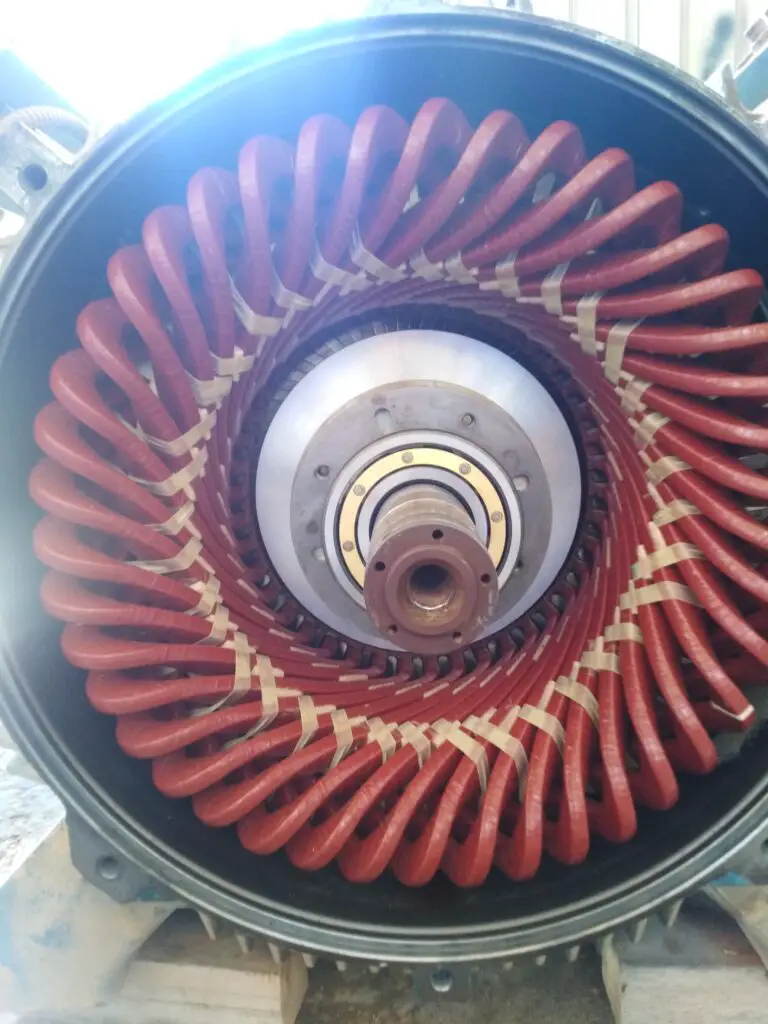
The only direct way to tell if a motor is drawing an overcurrent is the motor nameplate current or power rating. Measure the motor current it should be less than or equal to the motor nameplate.
But, the important question is, when should I doubt the motor current in the first place? When should I discover this issue?
It depends on whether the motor is in service or is new in service, even if it was connected but has been out of service for a long time.
Motors in service
Motor sound and temperature are the most common factors that give an early alarm about motor current!
Let me explain it to you, Two tasks of the motor PM are to check motor sound and temperature. If the motor noise is louder than normal, it may have a bearing issue, and then we check its current to find if it is overcurrent.
Many times, we have to bring the motor to the maintenance workshop to replace the bearing.
Motor temperature is another important sign of motor overcurrent issues. We thermal image motors during PM, if their temperature is high we check their current for overcurrent issues.
Motors newly connected
Whenever you connect the motor for the first time, or it is out of service for a long time, you should check its current and make sure it’s not drawing overcurrent.
How to prevent motor overcurrent?
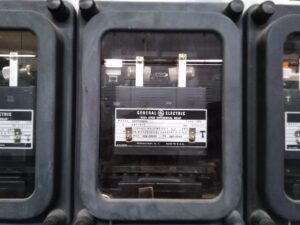
Motor current should be less than or equal to its nameplate current. I have discussed with you all the possible causes that overcurrent motors.
To prevent motor overcurrent, we simply prevent the reason behind it. Then, comes the protection devices like fuses, circuit breakers, and overcurrent relays.
Tips to prevent motor overcurrent:
- Choose the right motor rating. Motor power should be suitable for the mechanical load it’s intended to drive. If the motor power is lower than the load power, it will overcurrent.
- Check the motor nameplate before you start it the first time. Verify its power and voltage rating.
- Measure the motor current after connecting it, for the first time and after a long period out of service, and compare its current to the nameplate rated current.
- Check the motor overcurrent protection device, and verify its setting is suitable for the motor power. Thermal overcurrent protection should be set to 125% of the motor current according to the NEC, but keep in mind that some protection device manufacturers built in these 125% which means you should set the device to 100% of the motor current.
- Use undervoltage protection to protect the motor from voltage drop. Voltage drop is one of the overcurrent causes. Do not operate motors below 90% of nameplate voltage, as NEMA (The National Electrical Manufacturers Association), recommends.
- Use phase loss protection, when a motor loses one phase and only runs on two phases, it draws overcurrent and can burn out.
Don’t Leave Empty-Handed!
Install my Free Android App on Google Play:
Electrical Cables Most Common Tables “Cables Tables”
And, my Electrical Calculations App “Fast Electrical Calculator”
Discover more great content by subscribing to My channel
Looking to stay ahead of the game in the world of electrical engineering? Subscribe to my YouTube channel and gain access to exclusive content you won’t find anywhere else!
The staff I recommend
(Amazon Affiliate Links to products I believe are high quality):
- Economy 120 Volt/60Hz AC Power Source – Step-Down Voltage & Frequency Converters 1800W
- UNI-T Digital Multimeter Tester UT139C
- 50-Amp Extension Cord for RV “100ft”
- Voltage Stabilizer 110/220v
- Hair Dryer “best selling“
- TOSHIBA EM131A5C-BS Countertop Microwave Ovens
Disclaimer: This contains affiliate links to Amazon products. I may earn a commission for purchases made through these links.