Contactors are almost used in all control panels I see all the time in my work. Starting from small lighting control panels to medium voltage motor control panels.
No matter what voltage level the panel is, the contactor plays an essential role. In this article, I will provide you with important answers you should know. Let’s get started directly.
Table of Contents
difference between ac1 and ac3 contactor
AC1 and AC3 are two different classifications for contactors based on their intended usage and load characteristics.
These classifications are specified by the International Electrotechnical Commission (IEC) and indicate the type of duty or application for which the contactor is designed. Here’s a brief comparison between AC1 and AC3 contactors:
- AC1 Contactor:
- Application: AC1 contactors are designed for non-inductive or slightly inductive loads. They are typically used in applications with resistive loads or loads with a small amount of inductance, such as electric heaters, incandescent lighting, and other similar devices.
- Characteristics: AC1 contactors are suitable for duty cycles where the load is predominantly resistive, and there is minimal risk of significant arcing during switching. They are not intended for applications with motors or other inductive loads.
- AC3 Contactor:
- Application: AC3 contactors are designed for motor starting duty. They are specifically intended for applications where the contactor is used to start and stop electric motors. AC3 contactors are suitable for loads with high inrush currents, such as induction motors.
- Characteristics: AC3 contactors are built to handle the high initial currents associated with starting motors and can withstand the inductive kickback generated during motor stops. They are designed to handle the higher mechanical and electrical stresses associated with motor starting.
In summary, the main difference lies in the intended application and load characteristics:
- AC1 contactors are designed for resistive loads with minimal inductance, such as heating elements and lighting.
- AC3 contactors are specifically designed for motor starting duty, where the load is an electric motor with high inrush currents.
When selecting a contactor for a specific application, it’s crucial to choose one that matches the characteristics of the load to ensure optimal performance and longevity of the contactor.
Always refer to the manufacturer’s specifications and guidelines to determine the appropriate contactor for a particular application.
Will a bad contactor trip the breaker?
A bad or malfunctioning contactor itself may not directly trip a breaker, but it can contribute to issues that lead to breaker tripping.
A contactor is an electromechanical switch used to control the flow of electrical power to a load, such as a motor or lighting system.
If a contactor is faulty, it can cause problems that may lead to overcurrent or other electrical issues, triggering the circuit breaker to trip for protection. Here are some scenarios where a bad contactor might contribute to breaker tripping:
- Overcurrent Conditions:
- If the contactor is not functioning correctly, it may not be able to handle the current passing through it properly. This could lead to increased resistance, overheating, and potentially an overcurrent condition. Overcurrent protection devices, such as circuit breakers, are designed to trip when they detect excessive current to prevent damage to the electrical system.
- Arcing and Short Circuits:
- A faulty contactor may create arcing between its contacts during switching operations. Arcing can generate high temperatures and potentially lead to a short circuit. If a short circuit occurs, it can cause a sudden surge in current, prompting the circuit breaker to trip to protect the circuit.
- Failed Contactor Coil:
- The coil in the contactor is responsible for opening and closing the contacts. If the coil fails or is intermittently functioning, the contacts may not operate correctly. This could result in the contacts getting stuck in the closed position or not making proper contact, causing electrical issues that may lead to breaker tripping.
- Motor Overloads:
- Contactors are commonly used in motor control applications. If a contactor fails to open the circuit when the motor should be turned off, the motor may experience overloads. Overloaded motors can draw excessive current, triggering the circuit breaker.
- Faulty Wiring or Connections:
- A bad contactor might also be associated with faulty wiring or poor connections. Loose or damaged connections can increase resistance, generate heat, and contribute to overcurrent conditions.
If you suspect a contactor is malfunctioning or observe erratic behavior in the electrical system, it’s essential to address the issue promptly.
Regular maintenance, inspection, and replacement of faulty components can help prevent problems that might lead to breaker tripping and ensure the safe and reliable operation of the electrical system.
Always consult with a qualified electrician or technician if you encounter issues with electrical components.
Why exactly do we use contactors?
Contactors are used in electrical systems for several important reasons, primarily related to their ability to control the flow of electrical power to loads. Here are some key reasons why contactors are commonly used in various applications:
- Switching High Power Loads:
- Contactors are designed to handle high-current and high-voltage loads. They are commonly used to switch power to electric motors, lighting systems, heating elements, and other heavy-duty loads.
- Remote Control:
- Contactors allow for remote control of electrical circuits. They can be controlled by manual switches, pushbuttons, timers, relays, or programmable logic controllers (PLCs). This remote control capability is essential in industrial and commercial settings where operators need to control multiple devices from a central location.
- Reducing Wear on Switches:
- In applications where frequent switching is required, such as motor control, using a contactor can help reduce wear on manual switches. The contactor handles the high-current switching, extending the life of the smaller and less durable control switches.
- Motor Control:
- Contactors play a crucial role in motor control systems. They are used to start, stop, and reverse the operation of electric motors. Additionally, contactors can provide overload protection by integrating thermal overload relays that monitor the motor’s current.
- Power Factor Correction:
- In power distribution systems, contactors are used for power factor correction. They control the switching of capacitors to improve the power factor of the electrical system, optimizing energy efficiency.
- Lighting Control:
- Contactors are employed in lighting control systems, especially in large commercial or industrial buildings. They allow for centralized control of lighting circuits and can be integrated with automation systems to implement scheduled or occupancy-based lighting control.
- Reducing Arcing and Wear:
- Contactors are designed to minimize arcing during the opening and closing of contacts. This helps reduce wear and tear on the contacts, ensuring long-term reliability and safety.
- Automation and Integration:
- Contactors can be integrated into automated control systems, allowing for sophisticated control strategies. They are compatible with various control devices, enabling seamless integration into modern automation solutions.
- Protective Features:
- Contactors often incorporate protective features, such as thermal overload relays, to safeguard electrical equipment from overloads and prevent damage.
- Efficient Power Distribution:
- In power distribution panels and switchgear, contactors play a key role in efficiently distributing electrical power to different loads, ensuring that power is supplied where and when it is needed.
Overall, contactors provide a reliable and efficient means of controlling electrical power in a wide range of applications, contributing to the safe and effective operation of electrical systems.
Can we use the AC contactor for the DC supply?
Using an AC (alternating current) contactor for a DC (direct current) supply is generally not recommended.
AC and DC systems have different characteristics, and the components designed for one type of current may not be suitable for the other. Here are a few reasons why using an AC contactor for DC supply is not advisable:
- Arcing and Contact Wear: DC circuits tend to produce more arcing when contacts open or close compared to AC circuits. This arcing can lead to increased wear and tear on the contactor, potentially reducing its lifespan and reliability.
- Magnetic Saturation: AC and DC contactors have different designs to account for the differences in current behavior. DC contactors are often designed to prevent magnetic saturation, which can occur in AC contactors when used with DC. Magnetic saturation can lead to reduced efficiency and performance.
- Coil Ratings: The coil in a contactor is designed for a specific voltage and frequency. If you use an AC contactor with a DC supply, the coil may not operate correctly, leading to issues with the contactor’s functionality.
- Voltage Ratings: AC and DC systems often have different voltage ratings. Using a component with an incorrect voltage rating can result in malfunctions or damage.
If you need a contactor for a DC application, it’s recommended to use a contactor specifically designed for DC circuits.
DC contactors are designed to handle the unique characteristics of direct current, including managing arcing and preventing magnetic saturation.
Always consult the manufacturer’s specifications and guidelines to ensure that the contactor is suitable for your specific application.
Why do contactors have thermal ratings?
The maximum amount of rated current of the contactor, when controlling a thermal load (i.e. resistive load) is the contactor thermal rating. The thermal rating of the contactor is mentioned because the rating current of the contactor depends on the load type, inductive or resistive.
Contactor loads are categorized into:
Resistive loads AC1: These loads have almost unity power factor, like heaters and all thermal loads, so the contactor-rated current for these loads is called “Thermal current Ith”.
Inductive loads AC3: These loads are motor loads, which have inrush currents. The contactor has to make this high starting current.
The contactor thermal current rating, of AC1 loads, is greater than the rated inductive load current of the same contactor i.e AC3
For example: If we have a contactor of Ith 40 A for AC1 loads, and a rated current of 25 A for AC3 loads, this means that the contactor can control a heater up to 40A, and a motor up to 25 A only.
difference between the contactors and the circuit breakers
Contactors | Circuit Breakers |
A contactor use “connects” the device (load) with a high-power (voltage/current) supply. | A circuit breaker “breaks” the device (load) from the power supply. |
A contactor is a switching device/circuitry. | A circuit breaker is used for safety purposes. |
It depends on the coil voltage to act | It can act automatically in case of faults |
The contactor is a power-handling/ controlling device. | A circuit breaker is a piece of safety equipment. |
The arcing and flashing are handled at high power using the contactors. | The arcing or flashing in circuitry sets the circuit breaker to an OFF state. |
Not a device for automatic use. | The very need for a circuit breaker is to automatically power off the system. |
The basic rating for its use is its current rating. | The circuit breaker can sense the current as well as the voltage. |
We can’t use it to switch between states manually. | It can be turned off/on manually. |
Difference Between Contactors and Capacitor Contactor?
Contactors and capacitor contactors serve different purposes in electrical systems, and their designs are tailored to meet specific needs. Here are the key differences between contactors and capacitor contactors:
- Main Function:
- Contactor: A contactor is an electromechanical switch designed to control the electrical power circuit. It is commonly used to control motors, lighting, heating elements, and other loads. Contactors open and close electrical contacts to enable or interrupt the power flow to a load.
- Capacitor Contactor: A capacitor contactor, on the other hand, is specifically designed to switch capacitors in and out of an electrical circuit. Capacitors are often used in power factor correction systems to improve the efficiency of electrical networks by compensating for reactive power.
- Application:
- Contactor: Used in a wide range of applications to control various electrical loads, including motors, lights, and heaters.
- Capacitor Contactor: Primarily used in power factor correction systems where capacitors are employed to offset reactive power in industrial and commercial electrical systems.
- Design and Construction:
- Contactor: Designed to handle resistive loads and inductive loads like motors. The contactor’s construction is optimized for the switching of these loads.
- Capacitor Contactor: Specifically engineered to handle the unique requirements of capacitive loads associated with power factor correction. Capacitor contactors are designed to minimize arcing and ensure the reliable switching of capacitors.
- Handling Capacitive Loads:
- Contactor: While contactors can handle some capacitive loads, they are not specifically designed for applications where the primary load is a capacitor. Using a standard contactor for capacitor switching may lead to increased wear and reduced reliability.
- Capacitor Contactor: Designed to handle the high inrush current associated with switching capacitors. They are built to withstand the specific conditions associated with capacitive loads.
- Voltage and Current Ratings:
- Contactor: Rated based on the specific application, considering factors such as voltage, current, and duty cycle.
- Capacitor Contactor: Rated to handle the specific voltage and current requirements of capacitors used in power factor correction systems.
In summary, contactors are general-purpose switches used for controlling various electrical loads, while capacitor contactors are specialized switches designed specifically for the switching of capacitors in power factor correction applications.
Choosing the right type of contactor for a given application is crucial to ensure proper functionality and longevity of the electrical system.
I have written a detailed article about power factor correction, you can read it here.
electrical4uonline
How does a vacuum contactor work?
A vacuum contactor is a type of electrical contactor that utilizes a vacuum environment to extinguish the electrical arc generated during the opening and closing of its contacts.
This design provides advantages such as reliable switching, reduced maintenance requirements, and efficient performance, particularly in medium to high-voltage applications.
Vacuum contactors are commonly used in various industrial settings and power distribution systems.
Here’s a basic overview of how a vacuum contactor works:
- Contact Structure:
- A vacuum contactor typically consists of a set of main contacts and an operating mechanism. The main contacts are conductive materials that can be brought together or separated to allow or interrupt the flow of electrical current.
- Vacuum Enclosure:
- The contacts are housed in a vacuum-sealed enclosure. The vacuum serves as the dielectric medium between the contacts. Creating a vacuum helps to eliminate the presence of ionizable gases, which could lead to arcing.
- Operating Mechanism:
- The operating mechanism is responsible for opening and closing the contacts. It may involve a solenoid, motor, or other mechanical systems. When the contacts are closed, electrical current can flow through the system. When the contacts are opened, the operating mechanism creates a gap between the contacts.
- Arc Formation:
- When the contacts begin to open, an arc may form due to the electrical current continuing to flow across the gap. The arc is a luminous discharge of electricity across the separation between the contacts.
- Vacuum Arc Extinction:
- In a vacuum contactor, the vacuum plays a crucial role in arc extinction. As the contacts separate, the arc forms and the high-energy electrons in the arc collide with metal ions in the vacuum. This collision causes the metal ions to be emitted into the arc, creating a metal vapor. The metal vapor absorbs energy from the arc, helping to cool and extinguish it.
- Contact Separation:
- The operating mechanism continues to move the contacts apart until the arc is extinguished. Once the arc is extinguished, the vacuum helps prevent re-ignition by providing a high dielectric strength between the contacts.
- Contact Closure:
- When the contacts need to close again, the operating mechanism brings them back together. The vacuum environment ensures a clean and stable contact closure.
Advantages of Vacuum Contactors:
- High Dielectric Strength: Vacuum contactors offer excellent dielectric strength, making them suitable for high-voltage applications.
- Low Maintenance: The absence of gases and the sealed vacuum environment reduce wear and tear, resulting in lower maintenance requirements compared to some other types of contactors.
- Reliable Operation: Vacuum contactors provide reliable switching and are often chosen for critical applications where a high level of performance is required.
Vacuum contactors are widely used in various industries due to their reliable performance and ability to handle high-voltage applications.
What are the uses of vacuum contactors?
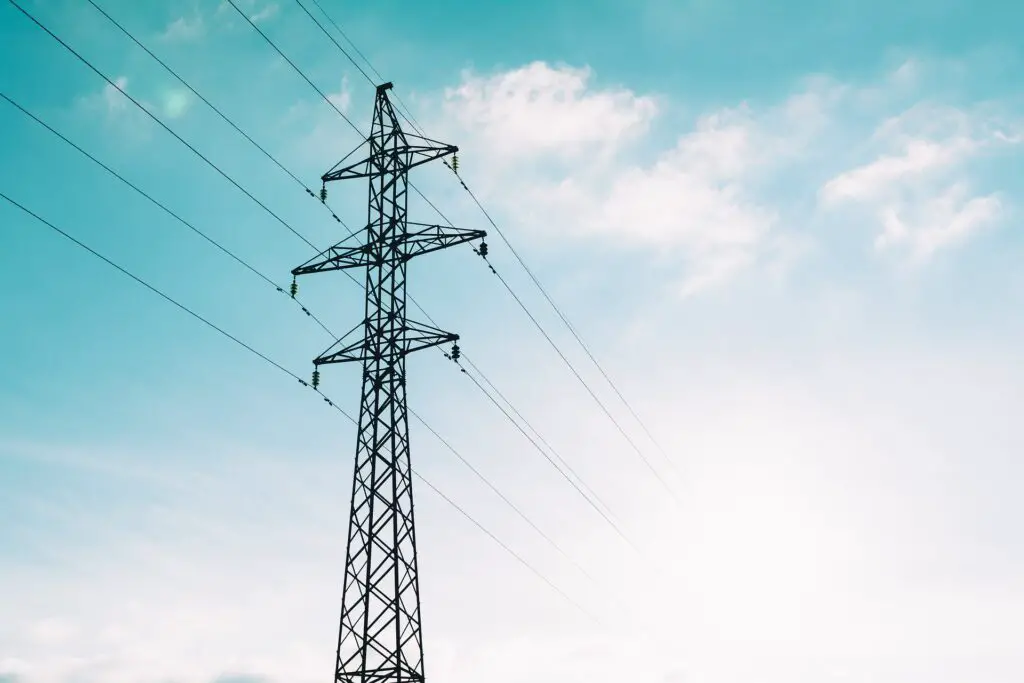
Vacuum contactors find applications in various industries and systems where reliable and efficient switching of electrical circuits is crucial. Here are some common uses of vacuum contactors:
- Motor Control:
- Vacuum contactors are frequently used in motor control applications, especially for medium to high-voltage motors. They provide reliable switching and control of the motor circuits, making them suitable for industrial processes, manufacturing facilities, and power plants.
- Power Distribution Systems:
- Vacuum contactors are employed in power distribution systems for switching and controlling electrical power at medium to high voltage levels. They are often used in distribution boards and switchgear for the reliable distribution of electricity in commercial and industrial facilities.
- Power Factor Correction:
- In power factor correction systems, vacuum contactors are used to switch capacitors in and out of the electrical circuit. This helps improve the power factor and overall efficiency of the electrical system, especially in industrial environments where power quality is critical.
- Lighting Control:
- Vacuum contactors can be utilized in lighting control systems, such as for switching large lighting loads in stadiums, auditoriums, or outdoor lighting installations.
- Mining Applications:
- Vacuum contactors are suitable for use in mining equipment, where the robust and reliable switching of electrical circuits is necessary in often harsh and demanding environments.
- Railway Traction Systems:
- Vacuum contactors are employed in railway traction systems to control the power supply to electric locomotives and trains. They help manage the acceleration, deceleration, and braking of electrically driven railway vehicles.
- Wind and Solar Power Generation:
- In renewable energy systems, such as wind and solar power generation, vacuum contactors can be used for switching and controlling the electrical circuits associated with power inverters and other components.
- Transformer Switching:
- Vacuum contactors are used in the switching of transformer circuits, particularly in medium to high-voltage applications. They ensure reliable and efficient switching during normal operation and maintenance activities.
- Arc Furnace Control:
- Vacuum contactors are employed in arc furnace control systems, where they play a crucial role in managing the electrical power supplied to arc furnaces used in industrial processes like steel production.
- Emergency Stop Systems:
- In critical applications where emergency stop systems are required, vacuum contactors can be used to quickly and reliably interrupt power in emergencies.
Don’t Leave Empty-Handed!
Install my Free Android App on Google Play:
Electrical Cables Most Common Tables “Cables Tables”
And, my Electrical Calculations App “Fast Electrical Calculator”
Discover more great content by subscribing to My channel
Looking to stay ahead of the game in the world of electrical engineering? Subscribe to my YouTube channel and gain access to exclusive content you won’t find anywhere else!
The staff I recommend
(Amazon Affiliate Links to products I believe are high quality):
- Economy 120 Volt/60Hz AC Power Source – Step-Down Voltage & Frequency Converters 1800W
- UNI-T Digital Multimeter Tester UT139C
- 50-Amp Extension Cord for RV “100ft”
- Voltage Stabilizer 110/220v
- Hair Dryer “best selling“
- TOSHIBA EM131A5C-BS Countertop Microwave Ovens
Disclaimer: This contains affiliate links to Amazon products. I may earn a commission for purchases made through these links.