Table of Contents
MCC meaning in electrical?
In electrical terminology, MCC stands for Motor Control Center. It is an assembly of one or more enclosed sections that house motor control units.
MCCs are used to control some or all of the electric motors in a facility, typically for industrial or commercial applications. Here’s a breakdown of its components and purpose:
MCCs provide a centralized location for motor control, protection, and monitoring, making it easier to manage multiple motors in a facility.
They are commonly used in manufacturing plants, refineries, commercial buildings, and various industrial settings to control motors responsible for tasks such as pumps, conveyors, fans, and other machinery.
Why is It Important to Have (MCC)?
Having a Motor Control Center (MCC) in industrial and commercial settings is important for several practical and safety-related reasons. Below are the key reasons why an MCC is essential:
1. Centralized Control
An MCC consolidates control of multiple motors into a single location, simplifying:
- Operation: Start, stop, and adjust motors from one area.
- Monitoring: Easily check motor status and performance.
- Maintenance: Access all motor controls in one place, saving time during repairs or inspections.
2. Improved Safety
- Electrical Isolation: MCCs include disconnect switches and breakers, allowing safe isolation of motors during maintenance.
- Fault Protection: Components like overload relays and circuit breakers prevent damage to motors and connected equipment during overloads, short circuits, or phase faults.
- Arc Flash Protection: Modern MCC designs comply with safety standards to minimize arc flash risks to personnel.
3. Motor Protection
MCCs are equipped with devices like:
- Overload relays to prevent overheating.
- Phase failure detection to protect motors from single-phasing.
- Short-circuit protection to limit damage during electrical faults.
This ensures longer motor life and reduces downtime.
4. Scalability and Flexibility
- Expandable: MCCs are modular and can accommodate additional motors or equipment as the facility grows.
- Customizable: They can be tailored to include specific control systems, such as variable frequency drives (VFDs) or programmable logic controllers (PLCs).
5. Operational Efficiency
- Energy Savings: With components like VFDs, MCCs optimize motor speed, reducing energy consumption.
- Reduced Downtime: Centralized control and diagnostic tools make troubleshooting faster, leading to fewer interruptions in production.
6. Compliance with Standards
Using an MCC ensures the system adheres to electrical safety and design standards, such as:
- IEC 61439 for low-voltage switchgear and controlgear assemblies.
- NFPA 70 (NEC) for safe electrical installations.
- Other local regulations and codes.
7. Enhanced Monitoring and Automation
- Smart MCCs: Modern MCCs integrate with advanced monitoring systems, allowing real-time data collection and remote control.
- Automation: Programmable controllers (PLCs) in MCCs facilitate process automation, improving productivity.
MCC panel Components
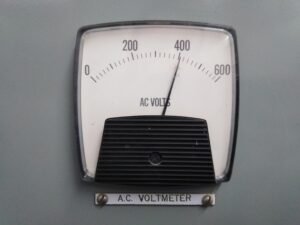
A Motor Control Center (MCC) panel is a standardized assembly that contains various components for the control and protection of electric motors.
These components are organized within the MCC panel to facilitate the operation, monitoring, and maintenance of electric motors.
Here are the key components typically found in an MCC panel:
-
Motor Starters: Motor starters are devices that provide the means to start and stop electric motors. They can include various types of starters such as:
- Full-Voltage Starters: These provide a direct supply of power to the motor.
- Reduced-Voltage Starters: These gradually apply voltage to the motor to reduce inrush current and mechanical stress during startup. Types include star-delta starters and autotransformer starters.
- Variable Frequency Drives (VFDs): VFDs are used for controlling the speed and torque of motors by varying the frequency and voltage supplied to them.
-
Overload Protection: Overload protection devices, such as overload relays or thermal overload heaters, are used to protect motors from excessive current and overheating. They can trip the motor starter in case of overloads or faults.
-
Control Devices: MCC panels include various control devices and components, including:
- Push Buttons and Pilot Lights: These are used for manual control, status indication, and fault indication.
- Selector Switches: These enable operators to select different motor operating modes, such as forward or reverse.
- Control Transformers: Control transformers step down voltage to power control circuits and devices safely.
-
Control Circuitry: MCC panels include control circuits that facilitate the operation of control devices, interlocking, and sequence control for motors.
-
Protection Devices: Protection devices ensure the safety of the motor and MCC. Common protection devices include:
- Circuit Breakers: These provide short-circuit and overcurrent protection for the entire MCC panel.
- Fuses: Fuses protect against overcurrent and short circuits in individual circuits.
- Ground Fault Protection: Ground fault protection devices detect ground faults and provide protection against electric shock hazards.
-
Busbars: Busbars are conductive bars that distribute electrical power from the incoming supply to the various motor starters within the MCC panel.
-
Interlocking Mechanisms: Interlocking systems prevent the simultaneous operation of conflicting motor starters, helping to avoid accidents and equipment damage.
-
Instrumentation: Depending on the complexity of the MCC panel, it may include instrumentation such as ammeters, voltmeters, and power meters to monitor electrical parameters and motor performance.
-
Communication and Networking: In modern MCCs, there may be communication interfaces or networking components to connect the MCC panel to a supervisory control system for remote monitoring and control.
-
Enclosure: The MCC panel is enclosed in a cabinet or enclosure to protect the components from environmental factors, dust, and physical damage.
The specific components and their arrangement within an MCC panel can vary depending on the application, the number of motors being controlled, and the design standards and requirements of the facility.
MCC Specifications
In the design and selection phase of MCC, design engineers specify the components of the panel.
Each MCC has its own requirements according to the application the motor is working on.
Some common components are in almost all applications. These are :
- Motor starter.
- Overload relay
- Circuit breaker and fusible switch.
- Start and stop buttons.
- Indicator lamps for each phase.
In one MCC, you may find each motor controller has its own control and protection devices as the design requires.
This panel in the image has many control devices, these devices control more than one load. It has the following control components:
- Circuit breakers.
- Contactors.
- Solid State relays (SSR).
- Control relays.
- PLC controllers.
Motor Control Center Manufacturers
This industry, I mean MCC manufacturing, is very large to list all manufacturers. But let’s list some of the leading companies.
- Allen-Bradley automation
- General Electric International Company (GE).
- WEG Industries.
- ABB Automation company.
- Siemens Automation.
- Eaton Corporation.
What is the difference between MCC and PCC panels?
The difference between MCC (Motor Control Center) and PCC (Power Control Center) panels lies in their functions, applications, and design features. Here’s a detailed comparison:
Aspect | MCC (Motor Control Center) Panels | PCC (Power Control Center) Panels |
---|---|---|
Purpose | Control and management of electric motors. | Distribution and control of electrical power to various loads and equipment. |
Components | – Motor starters – Overload protection devices – Control devices (push buttons, selector switches) – Control transformers – Control circuitry | – Circuit breakers – Switches – Relays – Busbars – Power meters – Protection devices |
Applications | Used to start, stop, control speed, and protect electric motors in industrial and commercial machinery. | Serve as the central point for power distribution and control in a facility, routing power to various electrical loads. |
Location | Typically installed near the machinery or equipment they control. | Usually located in dedicated electrical rooms or substations, separate from the equipment. |
Enclosure | Enclosure types vary depending on environmental conditions (e.g., NEMA 1, NEMA 12, NEMA 4X). | Housed in specialized enclosures designed for electrical protection and safety. Enclosure type varies based on application and location. |
This table highlights the main differences between MCC panels and PCC panels in terms of their purpose, components, applications, location, and enclosure types.
What is the difference between switchgear and MCC?
The difference between switchgear and a Motor Control Center (MCC) lies in their functions, components, and applications within an electrical power system. Here’s a detailed comparison:
1. Function
-
Switchgear:
Primarily used for power distribution, protection, and control in electrical systems. It protects electrical equipment from faults (like short circuits or overloads) and allows the isolation of circuits for maintenance.- Functions: Circuit switching, power isolation, and fault protection.
-
MCC (Motor Control Center):
Specifically designed to control and protect electric motors. It consolidates motor starters and related components in a centralized location.- Functions: Starting, stopping, protecting, and controlling motors.
-
Switchgear:
- Found in power generation plants, substations, and industrial/commercial buildings.
- Used for switching and protecting power lines, transformers, and loads.
-
MCC:
- Commonly used in industrial plants, HVAC systems, water treatment facilities, and other applications with multiple motors.
- Manages motor control and protection in a centralized manner.
-
Switchgear:
- Circuit breakers (Air, Vacuum, SF₆)
- Disconnect switches
- Relays and protection devices
- Busbars
- Lightning arresters
-
MCC:
- Motor starters (Direct-On-Line, Star-Delta, Soft Starters)
- Overload relays
- Circuit breakers for motor circuits
- Variable Frequency Drives (VFDs) (optional)
- Control transformers
-
Switchgear:
- Upstream in the system hierarchy.
- Typically located near power sources like transformers or generators, handling power distribution to various loads or MCCs.
-
MCC:
- Downstream in the system hierarchy.
- Receives power from switchgear or power distribution panels to control motors.
-
Switchgear:
- Operates at low voltage (LV), medium voltage (MV), or high voltage (HV) levels.
- Voltage levels depend on the application (e.g., HV for transmission systems, LV for local distribution).
-
MCC:
- Typically operates at low voltage (LV), ranging from 400-600V, as it directly supplies motors.
-
Switchgear:
- Built to handle high fault currents and ensure safety in power distribution systems.
- Designed for robust isolation, arc flash mitigation, and fault interruption.
-
MCC:
- Modular design to accommodate multiple motor control units in a compact space.
- Focused on motor-specific needs like starting, stopping, and speed control.
-
Switchgear:
- Protects the entire electrical distribution system.
- Includes fault current interruption, isolation, and overvoltage protection.
-
MCC:
- Protects individual motors from overloads, phase failures, and short circuits.
- Provides operational control to motors rather than system-wide protection.
Feature | Switchgear | MCC |
---|---|---|
Purpose | Power distribution and protection | Motor control and protection |
Location | Near power sources (e.g., substations) | Near motor loads |
Voltage | LV, MV, or HV | LV only |
Components | Circuit breakers, relays, busbars | Motor starters, relays, VFDs |
Applications | Power systems, substations | Industrial motor systems |
- Power Source (Generator/Transformer) → Switchgear → MCC → Motors.
What is a double-front MCC panel?
A double-front MCC panel is a type of Motor Control Center (MCC) where equipment and control components are installed on both the front and rear sides of the panel. This design maximizes the use of space and enhances accessibility in environments requiring compact yet efficient motor control setups.
Key Features of a Double-Front MCC Panel
- Two-Sided Access:
- Components are arranged on both the front and rear sides of the panel.
- Provides dual access for operation, maintenance, and troubleshooting.
- Space Optimization:
- Doubles the equipment density compared to a single-front MCC, saving floor space.
- Ideal for facilities with space constraints or high equipment density requirements.
- Compartments:
- Similar to single-front MCCs, it has segregated compartments for:
- Motor starters
- Circuit breakers
- Relays
- Variable frequency drives (if applicable)
- Each side is independently accessible.
- Similar to single-front MCCs, it has segregated compartments for:
- Busbar Placement:
- Typically located in the center of the panel between the front and rear sections.
- Ensures proper electrical separation and reduces the risk of faults.
- Ease of Maintenance:
- Dual access allows separate teams to work on front and rear components simultaneously.
- Reduces downtime during repairs or upgrades.
Applications of Double-Front MCC Panels
- Industrial Plants: Facilities with numerous motors, such as manufacturing, chemical, or petrochemical plants.
- Water and Wastewater Treatment Plants: Managing multiple pumps and motors in a compact space.
- HVAC Systems: For centralized control of fans, compressors, and other motors.
- Power Plants: Where efficient use of space is critical for motor control.
Advantages of Double-Front MCC Panels
- Higher Capacity:
- Can accommodate more motor control units compared to single-front MCCs.
- Space Saving:
- Ideal for environments with limited floor space.
- Improved Workflow:
- Allows multiple personnel to work on the MCC simultaneously.
- Cost-Effective for High-Density Systems:
- Reduces the need for additional MCC panels, saving installation and material costs.
Disadvantages
Higher Initial Cost:
- More complex design and installation compared to single-front MCCs.
- Requires Adequate Clearance:
- Needs sufficient space behind the panel for rear access, making it unsuitable for wall-mounted installations.
- Increased Complexity:
- Maintenance can be slightly more complicated due to the dual-sided arrangement.
In summary, a double-front MCC panel is an efficient solution for controlling multiple motors in high-density systems where space is a concern. It combines functionality and space-saving design, making it ideal for large industrial or commercial setups.
Unfortunately, the double-front MCC panel maintenance may be harder than a single-front one.
Don’t Leave Empty-Handed!
Install my Free Android App on Google Play:
Electrical Cables Most Common Tables “Cables Tables”
And, my Electrical Calculations App “Fast Electrical Calculator”
Discover more great content by subscribing to My channel
Looking to stay ahead of the game in the world of electrical engineering? Subscribe to my YouTube channel and gain access to exclusive content you won’t find anywhere else!
The staff I recommend
(Amazon Affiliate Links to products I believe are high quality):
- Economy 120 Volt/60Hz AC Power Source – Step-Down Voltage & Frequency Converters 1800W
- UNI-T Digital Multimeter Tester UT139C
- 50-Amp Extension Cord for RV “100ft”
- Voltage Stabilizer 110/220v
- Hair Dryer “best selling“
- TOSHIBA EM131A5C-BS Countertop Microwave Ovens
Disclaimer: This contains affiliate links to Amazon products. I may earn a commission for purchases made through these links.