Table of Contents
Why Use Different Starting Methods?
Motor starting methods refer to the techniques or systems used to initiate the operation of an electric motor. Starting a motor directly can cause issues like high inrush current, mechanical stress on the motor and the connected load, and voltage dips in the electrical network.
To avoid these problems, various starting methods are employed depending on the motor type, size, application, and load requirements.
Why Use Different Starting Methods?
- Reduce Starting Current: To avoid overloading the electrical network.
- Protect Motor and Load: To reduce mechanical stress on the motor and the connected machinery.
- Compliance with Utility Requirements: Many utility providers impose limits on inrush current to avoid network disturbances.
- Application-Specific Needs: Different loads (e.g., pumps, fans, compressors) require varying torque and speed characteristics at startup.
Motor starting methods
Stator Resistance starter
A Stator Resistance Starter (SRS) is a method used to start three-phase induction motors by adding external resistors to the stator circuit during startup.
This method helps reduce the starting current and torque, making it ideal for applications that need a smooth start and less mechanical stress.
The SRS setup includes resistors that are gradually removed from the circuit as the motor speeds up. Adding resistance at the start reduces the current and prevents voltage drops in the power supply. Once the motor reaches full speed, the resistors are completely bypassed, and the motor runs at its normal speed.
While this method provides a controlled start and reduces mechanical stress, it causes energy losses due to heat generated by the resistors. Proper sizing of the resistors is essential to minimize these losses.
Today, modern soft starters and variable frequency drives (VFDs) are more commonly used. They offer better efficiency, smoother control, and energy savings, making them a preferred choice over SRS in many applications.
Autotransformer Starter
An Autotransformer Starter is a reduced-voltage method used to start three-phase induction motors. It uses an autotransformer, which is a single-winding transformer that serves both the primary and secondary functions.
How It Works:
- During start-up, the motor is connected to the autotransformer, which supplies a reduced voltage.
- This reduced voltage lowers the starting current and torque, minimizing stress on the motor and the power system.
- Once the motor gains speed or reaches full speed, the autotransformer is bypassed, and the motor operates at full voltage.
Advantages:
- Provides a smooth and controlled start.
- Reduces mechanical and electrical stresses on the motor.
- Limits voltage drops and disturbances in the power network.
Disadvantages:
- Higher cost and larger size compared to simpler starters.
- Energy losses occur in the autotransformer itself.
This method is often used for large motors where controlling the starting current is essential to protect the motor and ensure power system stability. However, modern alternatives like soft starters and VFDs are becoming more common due to their efficiency and advanced control features.
Motor Soft Starter
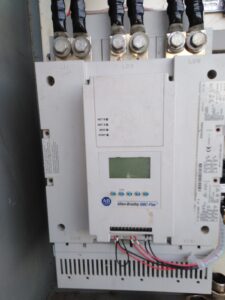
A soft starter is an electronic device designed to smoothly start and stop electric motors by gradually increasing or decreasing the voltage supplied to the motor. It is a popular solution to avoid the high inrush current and mechanical stress associated with direct-on-line starting.
How a Soft Starter Works
- Thyristors for Voltage Control: The soft starter uses components called thyristors (semiconductor devices) to control the voltage applied to the motor. These thyristors are arranged in pairs for each phase of the motor and work by adjusting the voltage through phase-angle control.
- Gradual Voltage Increase: At startup, the thyristors limit the voltage supplied to the motor. The voltage is gradually increased over a set time until it reaches full voltage. This allows the motor to “ramp up” smoothly to its operating speed.
- Deceleration (Optional): Some soft starters also provide a controlled stop, where the voltage is gradually decreased to avoid abrupt stops, which can stress the motor or the connected load.
Key Features and Benefits
- Adjustable Acceleration and Deceleration:
- You can program the ramp-up and ramp-down times to match the motor and load requirements. For example, a pump might need a slower ramp-up to avoid water hammer.
- Reduces Inrush Current:
- Without a soft starter, motors draw a high inrush current (up to 6–8 times the full-load current) at startup. A soft starter limits this, reducing the impact on the electrical supply network.
- Minimizes Mechanical Stress:
- A smooth start reduces sudden jolts to the motor and the connected machinery, increasing the lifespan of both.
- Compact and Simple:
- Soft starters are relatively small and easy to integrate into control panels, making them a convenient solution for many applications.
Typical Use Cases
Soft starters are ideal for applications that require controlled starting and stopping but don’t need precise speed control. Examples include:
- Pumps: To prevent water hammer and pipe stress during start and stop.
- Compressors: To reduce mechanical shock on the compressor’s moving parts.
- Conveyors: To prevent sudden jerks that could damage the load or the belt.
- Fans: To avoid high inrush currents in ventilation systems.
Limitations
While soft starters are excellent for managing starting and stopping, they do not provide speed control during normal motor operation. For applications that need variable speed control, a Variable Frequency Drive (VFD) would be more suitable.
Motor Star Delta Starter
A star-delta starter is a type of reduced-voltage starter designed to lower the starting current and torque in three-phase induction motors.
This method is ideal for applications requiring a smooth start and is especially suitable for larger motors. The name comes from the configuration of the motor windings during the starting process.
How It Works
- Star Configuration (Startup): At the beginning, the motor windings are connected in a star configuration. This reduces the voltage applied to each winding, which in turn lowers the starting current and torque.
- Delta Configuration (Normal Operation): After a set time or when the motor reaches a certain speed, the windings switch to a delta configuration, allowing the motor to run at full voltage.
This process minimizes the initial inrush current, reducing voltage dips in the power supply and mechanical stress on the motor and equipment during startup.
Advantages and Challenges
- Advantages: The star-delta starter effectively reduces starting current and torque, making it suitable for heavy-duty machinery like pumps and compressors.
- Challenges: It requires additional switching devices and control circuitry, which adds complexity and cost to the system.
This method remains popular for industrial applications where controlled starts are necessary to protect equipment and maintain power supply stability.
How Does A Star Delta Connection Work?
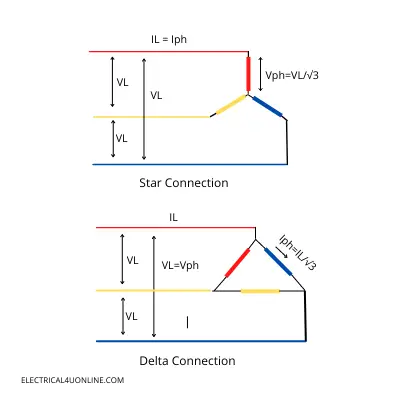
During motor startup, the motor windings are initially connected in a star configuration and then switched to a delta configuration.
This switching process is facilitated by a control and power circuit employing three contactors: one for the delta connection, another for the star connection, and the third for the main contactor.
Further in this article, you will come across the star delta starter control and power diagram.
Now, let’s find out How much star delta connection reduces the starting current.
At the star connection line Current is equal to the phase Current, While Voltage is not the same,
- IL = Iph
- Vph = VL/√3
Starting the motor in the Star connection reduces the voltage at starting to be just VL/√3, which is 58% of the motor-rated delta voltage.
Circuit Components of Y/∆ Starter
The star delta starter circuit consists of:
- Three contractors (Main contactor, Star connection, and Delta connection contractors)
- One timer
- Thermal overload for motor protection
- Start green colored push button.
- Stop the colored push button.
- Indicator lamps, Red, Yellow, and green for three-phase power. And one more orange for overload protection.
- Three-phase voltage volt-meter, and current-meter.
Star Delta Wiring and Circuit Diagram:
The Star Delta starter diagram is divided into power and control wiring. Both are in the following wiring diagram.
I’ve written a detailed article about Star Delta vs DOL Starter, read it now for more information.
DOL starter for motors
DOL starter or Direct online starter is the simplest method used for starting induction motors.
A Direct-On-Line (DOL) starter is a straightforward and cost-effective method for starting electric motors by connecting them directly to the power supply. It is typically used for smaller motors in applications where high starting current and torque are not a concern.
How a DOL Starter Works
- Direct Connection: The motor is connected to the power supply via a contactor and an overload relay.
- Full Voltage at Startup: When the contactor is energized, the full line voltage is immediately applied to the motor windings.
- High Inrush Current: This results in a surge of current (inrush current), which can cause voltage dips and mechanical stress on the motor and its connected equipment.
Advantages
- Simple design and easy to install.
- Cost-effective, with minimal components needed.
- Suitable for smaller motors where the power system can handle the high starting current.
Limitations
- High inrush current can lead to voltage dips, which may affect other equipment on the same power supply.
- Causes mechanical stress on the motor and connected machinery.
- Not ideal for larger motors, as the high starting current may destabilize the power system.
For larger motors or applications requiring smoother starts, advanced methods like soft starters or variable frequency drives (VFDs) are used. These alternatives help limit the starting current and provide better control over the motor’s speed and torque during startup.
What is the simplest of all starting methods for a motor?
The Direct-On-Line (DOL) starter is the simplest of all motor starting methods.
Why It’s Simple:
- The motor is directly connected to the power supply without any intermediate components to reduce voltage or current.
- It involves only a contactor to connect the motor and an overload relay to protect it from excessive current.
How It Works:
When the DOL starter is activated, the contactor closes, applying the full line voltage to the motor, which starts running immediately.
Key Features:
- Cost-effective: Minimal components and low complexity.
- Easy to use: Simple wiring and operation.
However, this simplicity comes with drawbacks like high inrush current and mechanical stress, which is why it’s generally used for smaller motors where these effects are manageable.
Which Motor starting method should I use?
The choice of motor starting method depends on several factors, including the motor size, the application requirements, and the power system’s capacity. Here’s a guide to help you decide:
1. Direct-On-Line (DOL) Starter
- Best For: Small motors (typically less than 5 kW or 7.5 HP) where high starting current and torque are not an issue.
- Advantages: Simple, cost-effective, easy to install.
- Limitations: Causes high inrush current, which can lead to voltage dips and stress on the motor.
2. Star-Delta Starter
- Best For: Medium-sized motors where a reduction in starting current and torque is needed.
- Advantages: Reduces inrush current and minimizes voltage dips.
- Limitations: More complex than DOL and not suitable for applications needing high starting torque.
3. Soft Starter
- Best For: Motors in applications requiring smooth starts, such as pumps, compressors, and conveyors.
- Advantages: Gradual voltage increase reduces mechanical stress and inrush current; adjustable acceleration and deceleration.
- Limitations: More expensive than DOL or Star-Delta; does not provide speed control during normal operation.
4. Autotransformer Starter
- Best For: Large motors (above 15 kW or 20 HP) where limiting starting current is critical for protecting the power system.
- Advantages: Reduces starting current while providing better torque than a star-delta starter.
- Limitations: Higher cost and size; energy losses in the transformer.
5. Variable Frequency Drive (VFD)
- Best For: Applications needing precise speed control, like fans, conveyors, and elevators.
- Advantages: Provides both smooth starts and speed control; highly efficient.
- Limitations: Expensive and more complex to install and maintain.
Key Considerations for Choosing:
- Motor Size:
- Small motors: DOL or Star-Delta.
- Medium to large motors: Star-Delta, Soft Starter, or Autotransformer.
- Very large motors: Autotransformer or VFD.
- Application Needs:
- Smooth start: Soft Starter or VFD.
- Precise speed control: VFD.
- Cost-sensitive: DOL or Star-Delta.
- Power System Capacity:
- If your system can handle high inrush current: DOL.
- If voltage dips are a concern: Soft Starter, Star-Delta, or VFD.
Don’t Leave Empty-Handed!
Install my Free Android App on Google Play:
Electrical Cables Most Common Tables “Cables Tables”
And, my Electrical Calculations App “Fast Electrical Calculator”
Discover more great content by subscribing to My channel
Looking to stay ahead of the game in the world of electrical engineering? Subscribe to my YouTube channel and gain access to exclusive content you won’t find anywhere else!
The staff I recommend
(Amazon Affiliate Links to products I believe are high quality):
- Economy 120 Volt/60Hz AC Power Source – Step-Down Voltage & Frequency Converters 1800W
- UNI-T Digital Multimeter Tester UT139C
- 50-Amp Extension Cord for RV “100ft”
- Voltage Stabilizer 110/220v
- Hair Dryer “best selling“
- TOSHIBA EM131A5C-BS Countertop Microwave Ovens
Disclaimer: This contains affiliate links to Amazon products. I may earn a commission for purchases made through these links.