Electric motors are an essential component of many industrial and commercial processes, powering everything from pumps and compressors to conveyor systems and manufacturing equipment.
However, like any machine, electric motors are subject to wear and tear over time, and if not properly maintained, they can suffer from a range of problems that can cause them to fail prematurely.
One of the most common issues that can affect electric motors is winding burnout, which can be caused by a range of factors, including electrical problems, mechanical issues, and environmental factors.
In this article, we will explore in detail the nine most common causes of motor winding burnout and discuss ways to prevent or address each of these issues to help ensure the longevity and reliable operation of electric motors.
Table of Contents
1. Overloading
Overloading is one of the most common causes of motor winding burns. When a motor is subjected to an electrical load greater than its capacity, the current flowing through the motor winding increases, causing the winding to overheat and eventually burn.
This can happen due to several reasons, such as excessive mechanical loads on the motor, voltage fluctuations, or incorrect motor sizing.
The overheating caused by overloading can damage the winding insulation, reducing its lifespan and increasing the risk of burnout.
Overloading can also cause the motor to run inefficiently, leading to increased energy consumption and reduced motor lifespan.
To avoid overloading, it’s essential to select a motor that is properly sized for the load it will operate under and to ensure that mechanical loads on the motor are within its rated capacity.
2. Voltage fluctuations
Voltage fluctuations, such as high or low voltage, can cause the motor winding to overheat and burn.
High voltage can cause the motor to draw excess current, while low voltage can cause the motor to stall and overheat.
These voltage fluctuations can occur due to problems with the power supply or due to voltage spikes caused by lightning strikes or other electrical disturbances.
To prevent voltage fluctuations from damaging the motor winding, it’s essential to ensure that the motor is properly connected to a stable and reliable power supply.
Voltage regulators, surge protectors, and other devices can also be used to protect the motor from voltage spikes and other electrical disturbances.
3. Electrical faults
Electrical faults such as short circuits or ground faults can cause excessive current to flow through the motor winding, leading to overheating and burning.
These faults can occur due to aging or damaged electrical components, improper installation, or incorrect wiring.
To prevent electrical faults from damaging the motor winding, it’s essential to ensure that the motor’s electrical system is installed correctly, with all connections and components properly secured and insulated.
Regular inspections and maintenance of the electrical system can also help identify and address potential issues before they cause damage.
4. Insulation failure
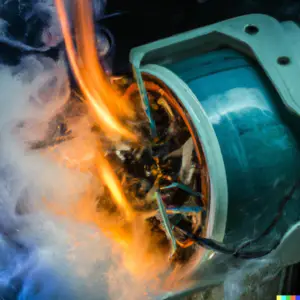
The insulation on the motor winding can fail due to aging, exposure to moisture or chemicals, or mechanical damage.
This can cause the winding to short circuit, leading to overheating and burning. Insulation failure can be caused by several factors, such as temperature cycling, thermal aging, or mechanical stress.
To prevent insulation failure, it’s essential to ensure that the motor winding is properly insulated and protected from environmental factors such as moisture, chemicals, and temperature fluctuations.
Regular inspection and maintenance of the insulation can also help identify and address potential issues before they cause damage.
5. Poor maintenance
Lack of regular maintenance can lead to the accumulation of dirt, dust, and other contaminants on the motor winding, reducing its heat dissipation capacity and increasing the risk of overheating and burning. Regular cleaning and inspection of the motor can help prevent such issues.
To prevent poor maintenance from damaging the motor winding, it’s essential to establish a regular maintenance schedule that includes cleaning, inspection, and repair of the motor and its components. This can help identify and address potential issues before they cause damage.
6. Bearing failure
When the bearings of a motor fail, it can cause the rotor to become misaligned, leading to increased friction and heat generation in the motor winding.
This increased friction can cause the winding to overheat and eventually burn. Regular bearing maintenance can help prevent such issues.
To prevent bearing failure from damaging the motor winding, it’s essential to establish a regular maintenance schedule that includes inspection and repair of the bearings and other motor components. Proper lubrication and alignment of the bearings can also help prevent bearing failure.
7. Misalignment
Misalignment between the motor and driven equipment can cause excessive mechanical loads on the motor, leading to overheating and eventually burning of the winding.
This misalignment can be caused by several factors, such as improper installation, worn or damaged couplings, or misaligned shafts.
To prevent misalignment from damaging the motor winding, it’s essential to ensure that the motor and driven equipment is properly installed and aligned.
Regular inspection and maintenance of the motor and driven equipment can help identify and address potential misalignment issues before they cause damage.
8. Wrong motor
Using a motor that is not designed for the load cycle type can cause the winding to overheat and burn.
Different motor types are designed to operate under different load cycle types, such as continuous, intermittent, or variable.
Using a motor that is not designed for the load cycle type can cause the motor to run inefficiently and increase the risk of winding burnout.
To prevent the wrong motor from damaging the motor winding, it’s essential to select a motor that is properly designed and rated for the load cycle type.
This can ensure that the motor operates efficiently and within its rated capacity, reducing the risk of overheating and winding burnout.
9. Environmental factors
Environmental factors such as high temperature, humidity, or corrosive chemicals can damage the motor winding insulation and increase the risk of winding burnout.
Exposure to such environmental factors can cause the insulation to break down or corrode, leading to a short circuit and overheating of the winding.
To prevent environmental factors from damaging the motor winding, it’s essential to protect the motor and its components from exposure to such factors.
This can include proper ventilation, insulation, and protection from moisture, chemicals, and temperature fluctuations.
Regular inspection and maintenance can also help identify and address potential environmental issues before they cause damage.
Read also my article: Hot or Cold? How Ambient Temperature Affects Your Motor
conclusion
In conclusion, electric motor winding burnout is a common problem that can cause costly downtime and repairs for industrial and commercial processes.
However, by understanding the common causes of winding burnout and taking proactive steps to prevent or address them, it’s possible to ensure the longevity and reliable operation of electric motors.
Whether it’s addressing electrical issues, maintaining proper lubrication, or protecting against environmental factors, regular inspection and maintenance can help identify and address potential issues before they cause motor winding burnout.
By implementing these preventive measures, organizations can minimize downtime, reduce repair costs, and ensure the smooth and efficient operation of their processes.
Don’t Leave Empty-Handed!
Install my Free Android App on Google Play:
Electrical Cables Most Common Tables “Cables Tables”
And, my Electrical Calculations App “Fast Electrical Calculator”
Discover more great content by subscribing to My channel
Looking to stay ahead of the game in the world of electrical engineering? Subscribe to my YouTube channel and gain access to exclusive content you won’t find anywhere else!
The staff I recommend
(Amazon Affiliate Links to products I believe are high quality):
- Economy 120 Volt/60Hz AC Power Source – Step-Down Voltage & Frequency Converters 1800W
- UNI-T Digital Multimeter Tester UT139C
- 50-Amp Extension Cord for RV “100ft”
- Voltage Stabilizer 110/220v
- Hair Dryer “best selling“
- TOSHIBA EM131A5C-BS Countertop Microwave Ovens
Disclaimer: This contains affiliate links to Amazon products. I may earn a commission for purchases made through these links.