A dry-type transformer is a type of electrical transformer that uses air or another non-liquid medium for cooling instead of oil or other liquid coolants. These transformers are commonly used indoors or in environments where fire hazards or environmental concerns make liquid-filled transformers less desirable.
Table of Contents
Why Do We Use Dry Type Transformers?
Dry-type transformers are used for various reasons and in a wide range of applications due to their specific advantages and characteristics. Here are some key reasons why dry-type transformers are used:
-
Fire Safety: One of the primary reasons for using dry-type transformers is their inherent fire safety. Unlike oil-filled transformers, which use flammable mineral oil, dry-type transformers use air or solid insulation materials (such as epoxy resin) for cooling and insulation. This significantly reduces the risk of fire, making them suitable for indoor installations and areas with strict fire safety regulations.
-
Environmental Considerations: Dry-type transformers are more environmentally friendly because they do not contain hazardous oils that can potentially leak and contaminate the environment. This makes them a preferred choice in environmentally sensitive locations, such as near water bodies or in regions with strict environmental regulations.
-
Indoor Applications: Dry-type transformers are well-suited for indoor applications, including commercial buildings, hospitals, data centers, tunnels, and industrial facilities. They are often used in locations where the risk of oil spills or leaks is unacceptable.
-
Maintenance Efficiency: Dry-type transformers generally require less maintenance compared to oil-filled transformers. There is no need to monitor oil levels, conduct oil testing, or deal with oil-related issues. This can result in lower operational costs over the transformer’s lifetime.
-
Compact Design: Dry-type transformers are available in compact designs, making them suitable for installations with limited space. They can be installed closer to loads without the need for special containment structures.
-
Environmental Considerations: Dry-type transformers are more environmentally friendly because they do not contain hazardous oils that can potentially leak and contaminate the environment. This makes them a preferred choice in environmentally sensitive locations, such as near water bodies or in regions with strict environmental regulations.
-
Longer Operational Life: Dry-type transformers often have a longer operational life compared to oil-filled transformers, as they are less prone to insulation degradation caused by oil impurities or heat.
-
Reduced Risk of Oil Leaks: Since dry-type transformers do not use oil, there is no risk of oil leaks or spills, which can be a significant concern with oil-filled transformers. This feature is especially important in areas where oil contamination is a risk to the local ecosystem.
-
Safety Regulations: In some regions and industries, safety regulations and codes may require the use of dry-type transformers, especially in buildings and facilities where fire safety is a top priority.
-
Noise Considerations: Dry-type transformers tend to produce less noise compared to oil-filled transformers, making them suitable for applications in noise-sensitive environments.
Advantages and disadvantages of dry-type transformers
Dry-type transformers offer several advantages and disadvantages compared to oil-type transformers.
These characteristics make them suitable for certain applications while limiting their use in others. Here are the key advantages and disadvantages of dry-type transformers:
Advantages of Dry-Type Transformers:
-
Fire Safety: Dry-type transformers are inherently safer in terms of fire risk because they do not use flammable oil as a cooling and insulating medium. This makes them suitable for indoor applications where fire safety is a concern.
-
Environmental Friendly: Dry-type transformers are more environmentally friendly as they do not contain hazardous oils that can potentially leak and contaminate the environment. They are easier to handle and dispose of at the end of their operational life.
-
Low Maintenance: Dry-type transformers generally require less maintenance compared to oil-filled transformers. There is no need to monitor oil levels or deal with oil quality. This can result in lower operational costs.
-
Compact Design: Dry-type transformers are available in compact designs, making them suitable for installations with limited space.
-
No Oil Leaks: Since there is no oil, there is no risk of oil leaks or spills, which can be a significant concern with oil-filled transformers.
-
Suitable for Indoor Use: Dry-type transformers are well-suited for indoor applications, including buildings, tunnels, and substations located in populated areas.
-
Longer Operational Life: Dry-type transformers often have a longer operational life compared to oil-filled transformers, as they are less prone to insulation degradation caused by oil impurities or heat.
Disadvantages of Dry-Type Transformers:
-
Limited Cooling Capacity: Dry-type transformers may have limited cooling capacity compared to oil-filled transformers. They may require forced air cooling systems, which can add to the cost and complexity of the installation.
-
Lower Overload Capacity: Dry-type transformers generally have lower overload capacity compared to oil-filled transformers of the same size. This means they may be less suitable for applications with frequent overloads.
-
Size and Weight: Dry-type transformers are typically larger and heavier than oil-filled transformers with the same power rating due to the need for larger cooling surfaces and insulation. This can be a disadvantage in installations with space constraints.
-
Higher Initial Cost: Dry-type transformers can have a higher initial purchase cost compared to oil-filled transformers, although this cost difference may be offset by lower maintenance and safety-related expenses over time.
-
Limited Voltage and Power Ratings: Dry-type transformers may have limited voltage and power ratings compared to large oil-filled transformers, which can make them unsuitable for certain high-power applications.
-
Noise Levels: Dry-type transformers can produce higher noise levels compared to oil-filled transformers, which may be a concern in quiet environments.
-
Reduced Efficiency at High Temperatures: Dry-type transformers may experience reduced efficiency at high ambient temperatures due to limited cooling capacity.
In summary, dry-type transformers are a preferred choice for applications where fire safety, environmental concerns, and minimal maintenance are critical factors.
Difference between Dry type and Oil type Transformers?
Dry-type transformers and oil-type transformers are two common types of electrical transformers used in various applications.
They differ primarily in their cooling and insulation methods, making them suitable for different environments and applications. Here are the key differences between dry-type transformers and oil-type transformers:
- Cooling Method:
- Dry-Type Transformer:
- Dry-type transformers use air or a solid insulation material (such as epoxy resin) to cool and insulate the windings.
- Cooling is achieved through natural convection (air circulation) or forced convection (using fans) inside the transformer enclosure.
- They are suitable for indoor applications where the risk of oil leaks or fires is a concern, as they do not contain flammable liquids.
- Oil-Type Transformer:
- Oil-type transformers use mineral oil or synthetic oil as a coolant and insulating medium.
- The oil serves both as a coolant and insulator, dissipating heat generated during operation.
- They are often used in outdoor or high-power applications where the heat dissipation requirements are greater.
- Dry-Type Transformer:
- Fire Safety:
- Dry-Type Transformer:
- Dry-type transformers are considered safer in terms of fire hazards because they do not contain flammable oil.
- They are commonly used in buildings, tunnels, and other indoor environments where fire safety is a concern.
- Oil-Type Transformer:
- Oil-type transformers use flammable mineral oil as a coolant and insulating medium, which poses a higher fire risk.
- Additional fire protection measures, such as containment systems and fire-resistant barriers, are often required when installing oil-filled transformers.
- Dry-Type Transformer:
- Environmental Impact:
- Dry-Type Transformer:
- Dry-type transformers are more environmentally friendly as they do not contain hazardous oils that can potentially leak and harm the environment.
- They are easier to handle and dispose of when they reach the end of their operational life.
- Oil-Type Transformer:
- Oil-filled transformers require special care and precautions to prevent oil leaks, spills, and contamination of soil and water.
- Spills or leaks of transformer oil can have adverse environmental impacts and may require costly cleanup efforts.
- Dry-Type Transformer:
- Maintenance:
- Dry-Type Transformer:
- Dry-type transformers generally require less maintenance compared to oil-filled transformers.
- There is no need to monitor oil levels or deal with oil leaks and oil quality.
- Oil-Type Transformer:
- Oil-filled transformers require regular monitoring of oil levels, quality, and insulation integrity.
- Maintenance includes oil testing, filtration, and occasional oil replacement to ensure proper operation and longevity.
- Dry-Type Transformer:
- Size and Weight:
- Dry-Type Transformer:
- Dry-type transformers are typically larger and heavier than oil-filled transformers with the same power rating due to the need for larger cooling surfaces and insulation.
- Oil-Type Transformer:
- Oil-filled transformers are more compact and lightweight for the same power rating, making them suitable for applications with space constraints.
- Dry-Type Transformer:
How Do You Test A Dry Transformer?
Among the routine tests that should be conducted on all dry-type power transformers are:
Dielectric Test:
The applied voltage waveform for single-phase should be roughly sinusoidal. The test must be carried out at the prescribed frequency.
Before disconnecting, the test voltage must be rapidly lowered to 1/3 of the maximum value. All of the windings must be tested. If no failure occurs at the ultimate test voltage, the test is considered successful.
Induced Voltage Test:
While performing this test, the test voltage must be double that of the rated voltage. It should be applied between the terminals of the secondary winding while keeping the primary winding open.
The test period at maximum voltage must be one minute, and the frequency must be double the rated frequency.
Voltage ratio measurement:
On all tap changer locations, voltage ratio measurements and polarity and connection checks must be done.
It’s also good to double-check the numbers allocated to the taps and the ratings. Measurement of voltage ratio must be done phase by phase between the terminals of matching windings. The voltage ratio is measured using the potentiometric approach.
Load Loss Measurement and No-load Current:
Supply LV windings are used to perform this test at the rated frequency and voltage. The waveform should be as close to a sine wave as feasible, and the primary windings should be open.
The frequency of the test must not deviate by more than 1% from the rated value. No-load current and loss, as well as the voltage’s mean and effective values, must be monitored.
The average value of three measurements taken by effective value ammeters will be used to calculate the no-load current.
When necessary, instrument transformers and transducers will be utilized to measure the power with three-watt meters.
Measurement of Winding Resistance:
When the windings are at ambient temperature and without power for a period of time sufficient to reach this State, winding resistance measurement should be done.
According to the measurements must be done in direct current between terminals. Temperatures in the surrounding environment must also be taken into account. It will be calculated as the average of three thermal sensor values.
Short Circuit Impedance:
The transformer’s performance is shown by the short-circuit loss and short-circuit voltage. The transformer’s HV windings are powered while the LV windings are short-circuited.
During the measurement, the current must be at IN or as near to this value as feasible. During the measurement, each phase’s voltage, current, and short-circuit losses should be monitored.
The measurement must be done quickly in order to prevent raising the winding temperature due to the applied current, and the measuring current must be kept between 25% and 100% of the rated current; by doing this, the measurement inaccuracies are caused by the rise in winding temperature will be reduced.
By performing all upper mentioned tests, you can ensure the proper operations of your transformer; if test values are not according to the correct operations values of the transformer conducted test will be considered failed, and you need to take the necessary measures to fix the fault to avoid any loss or incident.
What is Protection of Dry Type Transformers?
- Overcurrent Protection: Fuses and circuit breakers stop the current if it’s too high, shielding the transformer from overloads and short circuits. These are placed on both sides of the transformer.
- Temperature Monitoring: Transformers heat up during use. Sensors track temperature, and alarms go off if it gets too hot, preventing damage.
- Buchholz Relay: Only for oil-filled transformers, not used in dry-type ones since they don’t have oil.
- Pressure Relief: Rarely used in dry-type transformers. Sometimes included to release pressure and prevent rupture during faults.
- Grounding and Fault Protection: Proper grounding and devices like relays detect and fix ground faults quickly.
- Differential Protection: Detects internal faults by checking for current differences between the primary and secondary sides.
- Voltage Protection: Relays prevent damage from too-high or too-low voltage levels.
- Surge Arresters: These devices protect against voltage spikes from lightning or switching.
- Insulation Monitoring: Regular checks catch insulation issues early to avoid breakdowns.
- Remote Monitoring: Real-time systems track performance, helping operators act fast during problems.
The choice of protection depends on the transformer’s size, role, and importance. Proper design and regular maintenance ensure safe and reliable operation.
Read my other article, What is transformer mechanical protection.
Common Causes of Dry-Type Transformer Failure
Dry-type transformers are designed to be durable and reliable, but they can still fail for various reasons. Here are some common causes of failure in dry-type transformers.
- Overloading: Using a transformer beyond its rated capacity causes overheating, insulation damage, and eventual failure. This happens with sudden load changes or improper sizing.
- Insulation Degradation: Insulation weakens over time due to moisture, extreme temperatures, and contamination, increasing the risk of short circuits.
- Moisture Issues: Water entering the transformer harms insulation, leading to arcing and short circuits. Causes include humid environments, poor storage, or damaged seals.
- Voltage Surges: High voltage spikes from lightning or system faults can damage the windings and insulation.
- Contamination: Dust and dirt reduce cooling efficiency, causing hot spots that damage insulation and lead to failure.
- Aging: Transformers naturally wear out over time (20–40 years), with materials degrading and failure risks increasing.
- Mechanical Damage: Impacts or vibrations can harm internal components like windings or the core.
- Poor Maintenance: Irregular inspections and neglecting minor issues allow problems to grow, leading to major failures.
- Manufacturing Defects: Rarely, flaws in construction or materials can cause early failures, like poor winding connections or faulty insulation.
- Environmental Factors: Extreme heat, corrosive environments, or seismic events can stress the transformer and shorten its lifespan.
How to Prevent Failures
- Maintain Regularly: Perform inspections and tests to spot and fix problems early.
- Avoid Overloading: Operate within the transformer’s capacity.
- Protect Against Moisture: Use proper seals and store carefully in dry areas.
- Handle Carefully: Avoid physical impacts or excessive vibrations.
- Control the Environment: Shield from extreme temperatures, corrosive air, or other hazards.
Proper care ensures a longer, more reliable transformer life.
Read my other article about Transformer faults, for more information.
dry type transformer parts
A dry-type transformer, also known as a cast resin transformer or a non-liquid-filled transformer, is an electrical transformer that does not use any liquid coolant like oil.
Instead, it uses air or a solid insulation material to cool and insulate its components. The main parts of a dry-type transformer include
Transformer Core
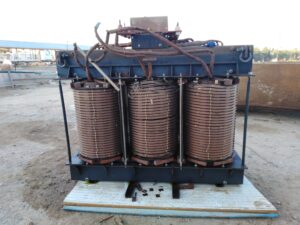
The core supports the primary and secondary windings by providing a low resistance channel for electromagnetic flux. It’s constructed by stacking thin sheets of high-grade grain-oriented steel separated by insulating material.
The Carbon content of the core steel is kept below 0.1 percent to keep hysteresis and eddy currents to a minimum. Eddy currents can be decreased when it is alloyed with silicon.
Transformer Winding
Primary and secondary windings are carried by the transformer for each phase. This winding comprises several turns of aluminum or copper conductors, which are separated from one other and the transformer’s core.
The form and configuration of transformer winding are determined by the current rating as well as the short circuit’s capacity, the strength of the circuit, the rise in temperature impedance, and surge voltages.
Transformer Insulation
Between the windings and the core, between the primary and the secondary windings, between each turn of the winding, and between all current-carrying elements and the tank, insulation is necessary.
It is imperative that the insulators have high dielectric strength, good mechanical properties, and be able to withstand high temperatures. Among the materials used to insulate transformers are synthetic materials, paper, cotton, and others.
Transformer Tank
The main tank is a component of a transformer. It serves two functions: one is to protect the core and windings from external influences, and secondly, it provides support to the other accessories of transformers. Fabrication of rolled steel plates into containers is used to create tank bodies.
As part of the package, lifting hooks and cooling tubes are included. Aluminum sheets are utilized instead of steel plates to save weight and prevent stray losses. On the other hand, Aluminium tanks are more expensive than steel tanks.
Transformer Bushings and Terminal
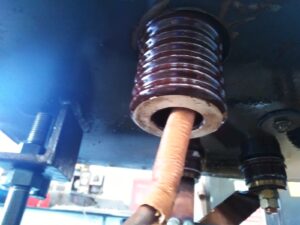
Bushings serve as insulators between the terminals and the tank. They’re affixed to the tops of the transformer tanks. They provide a safe path for the conductors that link terminals to windings.
Porcelain or epoxy resins are used to construct them.
Read my detailed article, Transformer bushing, what you should know.
Transformer Tap changers
Transformer’s secondary voltage is adjusted via tap changers. The transformer’s turns ratio is capable of being adjusted by these devices as needed. Two types of tap changers exist On-load tap changers and off-load tap changers.
On-load tap changers can work without stopping the current flow to the load, but off-load tap changers can only operate when the transformer is not providing any loads. There are also tap changers that change the taps automatically as per requirement. Transformer Air Ventilators.
Cooling System:
While dry-type transformers do not use liquid coolants, they rely on air for cooling. Some may have natural air cooling, where air circulates freely around the windings, while others may have forced air cooling, where fans are used to enhance the cooling process.
Don’t Leave Empty-Handed!
Install my Free Android App on Google Play:
Electrical Cables Most Common Tables “Cables Tables”
And, my Electrical Calculations App “Fast Electrical Calculator”
Discover more great content by subscribing to My channel
Looking to stay ahead of the game in the world of electrical engineering? Subscribe to my YouTube channel and gain access to exclusive content you won’t find anywhere else!
The staff I recommend
(Amazon Affiliate Links to products I believe are high quality):
- Economy 120 Volt/60Hz AC Power Source – Step-Down Voltage & Frequency Converters 1800W
- UNI-T Digital Multimeter Tester UT139C
- 50-Amp Extension Cord for RV “100ft”
- Voltage Stabilizer 110/220v
- Hair Dryer “best selling“
- TOSHIBA EM131A5C-BS Countertop Microwave Ovens
Disclaimer: This contains affiliate links to Amazon products. I may earn a commission for purchases made through these links.