Table of Contents
Why do transformers get hot?
Why Is Transformer Cooling Important?
Oil-Immersed Transformer Cooling Methods
What does the ONAN transformer mean?
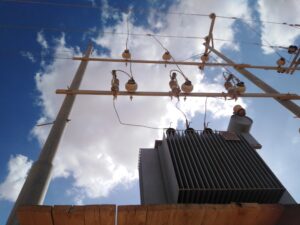
ONAN, short for Oil Natural Air Natural, is a common cooling method in power transformers. Here’s how it works:
-
Oil: The transformer is immersed in oil, which acts as both an insulator and a cooling medium. The oil absorbs heat generated by the transformer’s core and windings.
-
Natural Convection: As the oil heats up, it rises naturally, while cooler oil flows down to replace it. This cycle continuously transfers heat away from the transformer components.
-
Air Cooling: The heat absorbed by the oil is then released into the surrounding air. Transformers equipped with fins or radiators increase the surface area to improve heat dissipation. Warm air rises, carrying the heat away.
ONAN systems are widely used in oil-immersed transformers with low to moderate power ratings. They rely solely on natural convection, requiring no mechanical fans or pumps, making them cost-effective, simple, and reliable. However, for high-power transformers, more advanced methods like ONAF (Oil Natural Air Forced) or OFAF (Oil Forced Air Forced) are preferred to improve cooling efficiency.
How does ONAN transformer cooling work?
ONAN cooling advantages and disadvantages
Advantages of ONAN Cooling
-
High Reliability:
Since ONAN uses no moving parts like fans or pumps, there’s minimal risk of mechanical failure. -
Simplicity:
The system doesn’t require complex designs, control circuits, or temperature sensors, making it easy to implement. -
Low Maintenance:
Without fans or pumps, routine maintenance is significantly reduced, saving time and effort. -
Cost-Effective:
The absence of additional cooling equipment lowers initial costs, operating expenses, and maintenance costs.
Disadvantages of ONAN Cooling
-
Limited Heat Dissipation:
ONAN has a lower cooling capacity compared to systems that use forced air or oil circulation, such as ONAF or OFAF. -
Restricted Application:
Suitable primarily for lower-power transformers, as it may not efficiently cool high-power units.
For transformers with higher power ratings or operating in hotter environments, enhanced cooling systems like ONAF or OFAF are preferred for better efficiency.
ONAN vs KNAN transformer
Here’s a comparison of ONAN (Oil Natural Air Natural) and KNAN transformers in table format:
Aspect | ONAN Transformer | KNAN Transformer |
---|---|---|
Cooling Medium | Mineral oil | Kerosene (or other non-mineral oils) |
Environmental Impact | May have a higher environmental impact due to mineral oil. | Often chosen for reduced environmental impact and fire safety. |
Fire Point of Cooling Medium | Below 300°C | Above 300°C (higher fire point) |
Cooling Process | Natural convection within the oil and natural air circulation around the transformer. | Natural convection within the kerosene (or other non-mineral oil) and natural air circulation around the transformer. |
Safety | Generally considered safe but may pose a fire risk due to the lower fire point of mineral oil. | Offers enhanced fire safety due to higher fire point, making it suitable for hazardous areas. |
Transformer Size | Typically has a smaller footprint as mineral oil has lower heat dissipation capabilities. | Usually occupies a larger physical footprint because non-mineral oils dissipate heat more effectively. |
Temperature Tolerance | Components may have lower temperature tolerance due to the limitations of mineral oil. | Components can be designed for higher-temperature operation due to the superior cooling properties of non-mineral oils. |
Applications | Suitable for a wide range of applications and transformer classes. | Commonly chosen for applications with stringent fire safety requirements, such as hazardous locations (Zone 1 and Zone 2). |
Cost | Generally cost-effective. | Often more expensive than ONAN transformers due to the higher cost of non-mineral oils. |
Standards | Complies with relevant industry standards. | Complies with relevant industry standards. |
This table provides a side-by-side comparison of key aspects of ONAN and KNAN
What is an ONAF transformer?

Transformer ONAN and ONAF! What is the difference?
|
ONAN |
ONAF |
Oil Flow |
Natural |
Natural |
Air Flow |
Natural |
Forced With Fans |
Cooling efficiency |
Lower |
Higher |
Transformer Power |
One Rating Only |
More than One Power Rating depending on the Cooling fan stages |
Cost |
The lowest cooling method ever |
Higher |
Loading Capacity |
100% |
133% up to 167% |
Maintenance |
Not require |
Requires Fans Maintenance |
(OFAF) Oil Forced Air Forced transformer cooling
“OFAF” stands for “Oil Forced Air Forced” transformer cooling, which is a cooling method used in power transformers. In an OFAF transformer cooling system:
-
Oil: The transformer is immersed in oil, which serves as both an electrical insulator and a cooling medium. The oil helps dissipate heat generated during the transformer’s operation.
-
Forced Air: The “Forced Air” aspect indicates that the cooling process is enhanced by forcing or directing external air over the transformer’s cooling surfaces. Fans or blowers are used to facilitate this airflow, increasing the rate at which heat is dissipated from the oil and transferred to the surrounding atmosphere.
-
Forced Cooling: The combination of directed airflow and oil cooling creates an efficient forced cooling system. The forced air increases the heat transfer rate from the oil to the air, allowing the transformer to handle higher power ratings and heat dissipation requirements effectively.
OFAF cooling is commonly used in medium to large power transformers, where the combination of forced air and oil cooling allows the transformers to operate at their full rated capacity without overheating.
This method provides a more controlled and efficient cooling process compared to natural convection methods like ONAN (Oil Natural Air Natural) cooling.
(OFWF) Oil Forced Water Forced
“OFWF” stands for “Oil Forced Water Forced,” which is a cooling method used in power transformers. In an OFWF transformer cooling system:
-
Oil: The transformer contains oil as a cooling and insulating medium. The oil helps dissipate heat generated during the transformer’s operation.
-
Forced Water: The “Forced Water” aspect indicates that the cooling process involves actively circulating water through cooling tubes or coils within the transformer tank. Water is used as a coolant to remove heat from the transformer’s components.
-
Forced Cooling: OFWF cooling combines the use of forced water circulation with oil cooling to efficiently dissipate heat from the transformer. Water, as a cooling medium, has high heat-carrying capacity, making it effective at absorbing heat from the oil and the transformer’s core and windings.
OFWF cooling is often employed in large power transformers, especially those with high power ratings and demanding heat dissipation requirements.
The forced water circulation, along with the use of oil as an insulating medium, allows these transformers to operate at their full rated capacity without overheating.
This cooling method offers enhanced control and efficiency in managing the transformer’s temperature during operation.
(ODAF) Oil Directed Air Forced cooling
Dry-type transformer cooling methods
The only applied cooling methods of dry-type transformers are :
- Air Natural (AN). No cooling fans are used in this method, the natural airflow is enough to cool down the transformer.
- Air forced (AF). Fans are used to force airflow on the transformer body. This cooling method increases the transformer capacity up to 50%
There is no oil in dry-type transformers so, their cooling depends mainly on air. To make the air cool the transformer winding, the design is larger in size than an oil-immersed transformer, to make air flow easier between the windings.
If the dry-type transformer is located inside a closed enclosure, it should have good ventilation to circulate air and dissipate the heated air to the outside.
What is a Multistage Transformer Cooling System?
An electric transformer multistage cooling system is, a cooling system with cooling fans and oil pumps, that work in stages depending on the transformer temperature.
The multistage cooling system is automatically controlled by temperature sensors based electrical panel.
The cooling stage is depending on the transformer temperature rise. The control system controls the number of fans and pumps that should work.
ONAN cooling is the simplest cooling method. It also has no maintenance and a low noise level. But it is just for smaller transformers.
In the case of larger transformers, fans, and oil pumps are used to enhance the cooling. In this case, the transformer power rating is enhanced too, and it has more than one power rating.
What does it mean if a transformer has more than one power rating, 45/60/75 KVA?
If we have a transformer that has a power rating of 45/60/75 KVA, and a cooling method of ONAN/OFAF/OFAF, This means the transformer has a multistage cooling system and its power rating varies according to the cooling stage. In this case, the transformer power rating is:
- 45 KVA in case of ONAN cooling. No fans or pumps working.
- 60 KVA in case of operating the first stage of the ONAF cooling. A certain cooling number of units of fans and pumps works in this stage. In this stage no need to operate all fans and pumps.
- 75 KVA when ONAF cooling is fully operated. i.e. all cooling fans and pumps are fully operated. The transformer temperature rise is higher than the rise in the first stage.
Loading capacity for multistage cooling transformer:
Loading Capacity | Type Of Cooling |
100 % | ONAN |
100-133% | ONAN-ONAF |
100-133-167% | ONAN-ONAF-ONAF |
100-133-167% | ONAN-ONAF-OFAF |
125% | ONWF |
167% | OFWF |
I have written an article answering important questions about transformer cooling. I highly recommend you read it here.
Don’t Leave Empty-Handed!
Install my Free Android App on Google Play:
Electrical Cables Most Common Tables “Cables Tables”
And, my Electrical Calculations App “Fast Electrical Calculator”
Discover more great content by subscribing to My channel
Looking to stay ahead of the game in the world of electrical engineering? Subscribe to my YouTube channel and gain access to exclusive content you won’t find anywhere else!
The staff I recommend
(Amazon Affiliate Links to products I believe are high quality):
- Economy 120 Volt/60Hz AC Power Source – Step-Down Voltage & Frequency Converters 1800W
- UNI-T Digital Multimeter Tester UT139C
- 50-Amp Extension Cord for RV “100ft”
- Voltage Stabilizer 110/220v
- Hair Dryer “best selling“
- TOSHIBA EM131A5C-BS Countertop Microwave Ovens
Disclaimer: This contains affiliate links to Amazon products. I may earn a commission for purchases made through these links.