Electrical isolation is one of the most important tasks in our work. It should be done only by qualified persons to ensure a safe working and incidents-free workplace.
I always double-check the isolation myself before starting any maintenance or repair work.
Table of Contents
What is electrical isolation (Lockout Tagout)?
Electrical Isolation (Lockout Tagout – LOTO) refers to a safety procedure used to ensure that electrical equipment is properly shut off and cannot be started up again until maintenance or servicing is completed.
This practice is critical for protecting workers from unexpected energy release, which could lead to injuries or fatalities.
Key Components of Electrical Isolation and LOTO
-
Electrical Isolation
Electrical isolation involves disconnecting electrical equipment from the power source to prevent the flow of electrical energy. This typically requires:- Turning off circuit breakers or switches.
- Verifying that the equipment is de-energized.
- Applying safety measures such as grounding or insulating exposed wires.
-
Lockout
A physical locking mechanism is applied to the power isolation device (e.g., a switch or breaker) to ensure it cannot be turned back on without proper authorization. Only authorized personnel with the corresponding key or combination can remove the lock. -
Tagout
A clearly visible tag is attached to the isolation point to warn others that the equipment is being serviced and must not be operated. The tag includes information such as:- The name of the person performing the work.
- The date and time the tag was placed.
- Instructions or warnings.
Steps in a Typical LOTO Procedure
-
Preparation
- Identify all energy sources connected to the equipment.
- Understand the risks involved in the task.
-
Shutdown
- Turn off the equipment using the normal operational controls.
-
Isolation
- Disconnect the equipment from its power source by operating switches, breakers, or valves.
-
Lockout/Tagout Application
- Attach locks and tags to the isolation points.
-
Release Stored Energy
- Drain or release any residual or stored energy (e.g., capacitors, springs, hydraulic pressure).
-
Verification
- Test or visually confirm that the equipment is completely de-energized before beginning work.
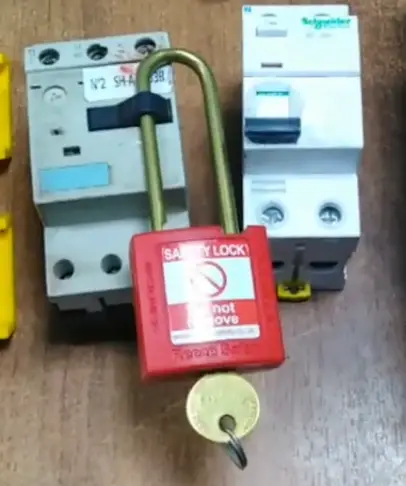
What is the difference between lockout and tagout?
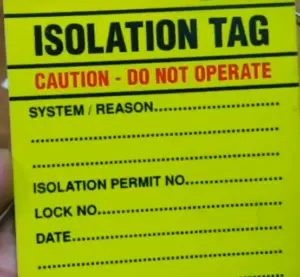
Lockout refers to the placing of an electronic lock on a device which prevents the release of energy.
Tagout is the act of using an identification tag on a switch or any other device that is isolated to warn others against starting this piece of equipment.
Locking out is meant to stop machinery or equipment’s sudden start-up or activation during maintenance and service operations. Tagout is only employed with lockout, except when it is not possible.
While being serviced or maintained, equipment should be locked out. Accidents involving machinery that is being fixed but is not locked out frequently result in significant injuries such as amputations, fractures, and even death.
When repairing or modifying machinery, it is critical to lock out and tag electricity at its source to guarantee that power does not reach the machinery.
How is Lockout and Tagout removed?
The procedure for the removal of Lockout and Tagout (LOTO) involves a series of steps to ensure that re-energizing equipment is done safely and systematically. Here’s a general outline:
Inspection and Preparation
- Verify Completion of Work: Ensure all maintenance or servicing tasks are finished, and all tools, materials, and personnel are clear of the work area.
- Inspect the Equipment: Confirm that the equipment is intact and ready for operation.
Notify Affected Personnel
- Inform all personnel involved in or affected by the LOTO process that the equipment will be re-energized.
Remove Locks and Tags
- Authorized Personnel Only: The same individual(s) who applied the lock and tag must remove them, unless a special process is followed to authorize removal by another person.
- Check for Obstructions: Ensure that no objects are interfering with the isolation devices or the equipment.
Restore Power
- Reconnect the equipment to the energy source following the proper sequence.
- Use normal operating controls to turn the equipment back on.
Test and Observe
- Run the equipment to ensure it is functioning as expected.
- Monitor for any abnormal conditions or issues.
Final Notification
- Inform all affected personnel that the equipment is now operational and back in service.
Important Notes
- If the original person who applied the lock is unavailable to remove it, a formal procedure involving management approval must be followed.
- Never bypass a lock or tag without proper authorization, as this could result in severe safety hazards.
By strictly adhering to these steps, the risk of accidents during re-energization is minimized, and workplace safety is upheld.
I have written a detailed article about LOTO on my other safety frenzy site you can read it here.
Who are affected employees in a lockout/tagout?
Affected employees in a Lockout/Tagout (LOTO) context are workers whose jobs require them to operate or use equipment that is being serviced or maintained under LOTO or work in areas where such procedures are being performed. They are not directly involved in applying or removing the LOTO devices but must understand the importance of these safety measures.
Examples of Affected Employees:
- Operators of the equipment being serviced.
- Workers in the vicinity of the locked-out equipment.
- Employees who may attempt to restart equipment without realizing it is under maintenance.
Key Responsibilities of Affected Employees:
- Avoid tampering with LOTO devices.
- Understand the purpose of the LOTO and follow all instructions provided by authorized personnel.
- Stay clear of equipment under maintenance unless authorized.
Proper communication and training are essential to ensure that affected employees are aware of their roles in maintaining a safe workplace.
Don’t Leave Empty-Handed!
Install my Free Android App on Google Play:
Electrical Cables Most Common Tables “Cables Tables”
And, my Electrical Calculations App “Fast Electrical Calculator”
Discover more great content by subscribing to My channel
Looking to stay ahead of the game in the world of electrical engineering? Subscribe to my YouTube channel and gain access to exclusive content you won’t find anywhere else!
The staff I recommend
(Amazon Affiliate Links to products I believe are high quality):
- Economy 120 Volt/60Hz AC Power Source – Step-Down Voltage & Frequency Converters 1800W
- UNI-T Digital Multimeter Tester UT139C
- 50-Amp Extension Cord for RV “100ft”
- Voltage Stabilizer 110/220v
- Hair Dryer “best selling“
- TOSHIBA EM131A5C-BS Countertop Microwave Ovens
Disclaimer: This contains affiliate links to Amazon products. I may earn a commission for purchases made through these links.